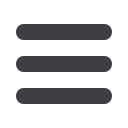

March 2017
•
MechChem Africa
¦
11
⎪
Pump systems, pipes, valves and seals
⎪
Motor rating
110 kW
Pump discharge pressure
640 kPa
Pressure downstream of the valve
380 kPa
kWwasted
= (640-380)/640×110 = 44.7 kW
Energy wasted
= 44.7×8 760×0.9×R0.90/kWh = R317 000 per year
Table 1: A table showing how much energy and money is wasted by throttling a pump and how much
money can be made available to fix the problem. A 90% utilisation factor is assumed.
Pumps are often throttled to limit the current
drawn by the pump motor. In many the original
reason for doing this is forgotten and it is no longer
necessary.
have just read the maximum value from the
technical spec sheet incorrectly.
The solution? Open the valve and see if
there are any adverse effects on the pump
or motor. The energy savings can be quite
stupendous.
In a parallel pumping case study for a steel
mill cooling water system, for example, six
pumps were operating in parallel, providing
cooling water into a steel mill. All the pumps
were throttled to between 25 and 50% open
to ensure the current neverwent above 73A,
even though the rated current for themotors
was found to be 85 A.
When opening the valve on one pump to
100%, we observed that the current never
went higher than 79 A, well within the rated
capacity. We were able to achieve the same
flowrate(actuallyslightlyhigher)withonlyfive
pumps running. And shutting down one pump
reduced the total power drawn by 258 kW.
These pumps have since been running
in this state for over a year with no adverse
effects on the motors, resulting in saving of
over R1.5-million/year in electricity costs and
2 050 000 kWh per year in energy savings.
Identifying energy-saving opportunities
fromthrottled pumps is actually easy. All that
is needed is a stroll through the plant with
your eyes open.
• Look for control valves with pressure
gauges upstream and downstream of the
valve and use the formulas outlined here
toestimate thewastage through the valve.
• Look for ammeters showing pumps are
drawing maximum amps – these pumps
are, most likely, being throttled.
• Question every answer you get and never
assume the original reasons are still valid.
If you discover that any pump is being throt-
tled, the first question is, does it need to be? If
it is onlybeingdone to limit themotor current,
then it is often unnecessary. Open the valve
and see what happens.
If there is a valid reason for throttling the
pump, then two far better andmore economi-
cal options are available to pump operators.
The first is to trimthe pump impeller. Thiswill
return the pump’s operating point to the duty
point of system, saving significant amounts of
energy and money.
The second solution, which is slightlymore
expensive but still highly cost-effective, is to
reduce the pump speed by using a variable
speed drive (VSD).
There arenogood reasons to continuously
throttle pumps. Not only are you throwing
electrical energy and money away, but also
the reliability of the pumps always suffers
if they are operated too far away from their
duty points.
q