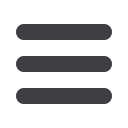

34
M
ARCH
2016
T E CHNOLOG Y
Suite of digital hand tools
PRECISION measurement specialist
Optical Metrology Services has
launched a comprehensive portfolio of
compact digital hand tools. Developed
to improve project efficiencies in the
field, the range ensures fast, accurate
and repeatable electronic assessment
of pipeline geometry.
Durable, portable and designed with
the user in mind, the suite comprises
eight individual quality assurance tools.
Developed in-house by OMS’s team
of precision measurement technology
experts, each unit offers a real-time
solution to overcome challenging
pipeline fit-up and welding requirements.
From pipe ovality, end squareness
and pipe straightness, to girth weld
integrity and bevel alignment, the next-
generation portfolio provides a solution
for on-site pipe measurement. Videos
highlighting the tools’ capabilities in
detail, as well as a brief introduction to
their application, are available to watch
at
www.youtube.com/omsmeasureCommenting on the launch, Hugh
Davies, director of client solutions
at OMS, said, “With precision
measurement key to the success of any
pipeline project, we wanted to introduce
a comprehensive solution to help quality
control managers, welders, pipe mills
and coating yards to ensure that the
various pipe features are all within
specified project tolerances.”
Optical Metrology Services
– UK
Email:
info@omsmeasure.comWebsite:
www.omsmeasure.comPrecision laser tube forming and welding
THE Machines of Yvonand, Switzerland,
is not only known for its decades of
experience in the manufacture of
extrusion lines for drip irrigation pipe and
tube systems, but also for its know-how
and expertise in the field of transverse
and longitudinal laser welding of flat
sheet and tubular formed metals,
as well as multi-layer metal polymer
combinations.
The traditional processing of metal
tape in the thickness range of 0.05 to
1mm in metal forming and stamping
plants is still discontinuous, or for
thicknesses above 0.15mm is covered
with other technologies requiring high
energy consumption and forming or
shielding gas, which is often a concern
to the industry.
THE Machines has continued to
drive forward both technologies of
laser cross welding and continuous
laser longitudinal welding in the field
of protection-gas-free laser welding
of any aluminium alloy, and the high
performance welding of a wide range of
alloys including stainless steel, Cr and Ni
alloys, copper, titanium and composites
of these and plated products.
A discontinuous process means
that a coil change mandates not
only a machine stop, but also a time-
consuming setup procedure each time
when re-threading the new tape. This
interruption of production could be
drastically reduced by combining the
end of the tape with the incoming strip
of the new coil in such a way that the
weld and seam fully meets the rigorous
requirements of the subsequent process
steps, eg line tensions, repeated
bending, forming or heat treatment, at
full production speed and securely. The
actual seam can subsequently be left in
the final product or cut out.
This optimisation potential has as yet
remained untapped, since no suitable
welding method for joining the ends of
thin metal strips was available on the
market to meet these requirements.
THE Machines, familiar for years
with laser technology and protection-
gas-free laser welding and the welding
of thin-walled metal sheets, offers
solutions for cross-welding with the
SLT range of machines. The series
covers a bandwidth as standard from
80 to 750mm (higher bandwidths
available on request). Laser welding is
particularly suitable for processing thin
sheets where other methods would
fail. The welding is conducted in fully
automated process steps. Depending
on the materials and thicknesses,
pre-programmed welding parameters
guarantee high, repeatable quality.
The tensile strength and elongation at
the seam are generally ≥85 per cent of
the base material. In combination with
tape accumulators of the ABH series
each non-continuous process could be
changed into a continuous process to
raise the productivity of existing lines.
Applications for cross welding and butt
joining of alloys ranging from 0.05mm
(50 micron) are found in steel and
alloy producers, precision metal strip
suppliers, stamping operations, plating
operations and continuous tube forming
and welding operations. A number of
novel and custom-made solutions are
available to meet market demands.
The LSL range of longitudinal laser
welding equipment is available in the
machine types 40, 63 and 110 for
composite tube diameters up to 40mm,
63mm and 110mm, and a very compact
12mm version for high precision and
performance formed and welded tubular
metal structures.
Especially micro precision tubes below
2mm OD and with wall thicknesses
down to 0.05mm can be produced
in-line in one single production step.
These are used in medical applications
(needles) and as heat exchangers in the
aeronautic and aerospace industry.
Other applications range from
capillary tubes to tubes for industrial and
automotive industries, as well as tubes
containing optical fibres such as used
in OPGW, FIST and other fibre optic
applications.
Speciality LSL lines can be custom
adapted for tube forming and laser
welding of products with a complex ratio
of wall thickness to weld diameter. The
equipment is supplied with a disc-laser
source, which is low in maintenance
requirements. High process speeds
up to 50m/min are guaranteed with
an integrated optical seam tracking
system.
The quality of the entire seam integrity
and full weld depth and volume are
checked using the latest multi-channel
remote field eddy current testing. The
system uses a non-destructive testing
and in-line inspection of the weld seams
with a very high sensitivity to detect
small and even hidden defects.
THE Machines Yvonand SA
–
Switzerland
Email:
info@the-machines.chWebsite:
www.the-machines.ch