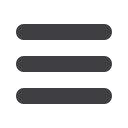

Abbreviations/Acronyms
DOL – Direct Online
IEC
– International Electrotechnical Commission
MTL
– Motor Terminal Latency
PF
– Power Factor
VFD
– Variable Frequency Drive
VSD
– Variable Speed Drive
electricity consumption; industry accounts for 64% of this, the
commercial sector for 20% and the residential sector 13% general
purpose industrial electric motors of between 0,75 kWand 375 kW
consumed 4 700 TWh (68% of the total for all motors); their share
of global electricity demand is 30%
• The three economies with the highest electricity consumption for
motors are China, the USA and the European Union which col-
lectively consumed 4 000 TWh (56% of global electricity demand
for motors); the addition of four more countries (Japan, Russia,
Canada and India) adds another 1 200 TWh (18%), which makes
a total of 5 200 TWh (74%)
• The net mechanical energy used in motor applications is esti-
mated to be roughly 50% of the electrical energy input intomotors
(e.g. on average it is thought electric motor systems operate at
an efficiency of about 50%). The losses occur in the motors them-
selves as well as in throttles and dampers, gears, transmissions,
clutches, brakes, VFDs, etc. [2]
It is estimated that 67,6% of electricity use by electric motors falls
into the medium range between 0,75 and 375 kW, (I believe this is
actually between 7,5 kW and 375 kW as although the number of small
motors (0,75kw to 7,5 kW) in operation is very large these motors
tend to be largely in the domestic market and therefore have very
low operating hours in a year [3].
Energy-saving technologies and saving potentials
The most obvious is improvement of component efficiency.
Ac induction motors
Standard ac cage induction motors are probably the cheapest and
most effective means of converting electrical energy into rotational
mechanical power.
Medium sized motors (7,5 to 375 kW)
The medium range of motors, the largest user of electric power, are
manufactured in standard sizes and traded on the world market as a
standard, interchangeable product. These products are manufactured
to various international standards which means motors from any
particular supplier are exchangeable.
Most manufacturers manufacture the motors to meet the require-
ments of the International Electrotechnical Commission (IEC) specifi-
cations, including efficiency. The efficiency classes that cover motors
DRIVES, MOTORS + SWITCHGEAR
from 0,75 kW to 375 kW, 2 pole, 4 pole, and 6 pole, for both 50 Hz and
60 Hz. The losses in an ac induction motor consist of the following:
• Stator losses
• Rotor losses
• Core (iron) losses
• Stray (additional load) losses
• Friction and windage (mechanical losses)
If each of these points is studied individually, there is always the pos-
sibility to reduce the losses in that component. Care must be taken,
as changing materials or components can have other effects on the
motor performance and characteristics.
Figure 2: Typical induction motor showing components for potential
improvements of efficiency.
All this is relevant but if the motor is operating at 94% or 95% the
possible increase in efficiency is going to be small; and 1% increase
from 94 to 95% in efficiency of a 55 kW motor running at full load is
only going to save 0,616 kW, operating for 300 days a year and eight
hours per day. a total of 1 478 kWh − financially not a great amount,
but a saving.
Lower range of induction motors (0,75 to 7,5 kW)
There is a large number of these motors in use but the power con-
sumed is relatively small. In this range you findmotors used in domes-
tic applications where the usage is low and the efficiencies relatively
poor − but the total power consumed is very small. These motors are
generally mass produced and have poor efficiency … as low as 60%.
Limiter Power Management System
(patent pending)
A motor power management system which optimises the
energy consumption and lifespan of electric induction motors
using the technology is available owing to the advances in
power electronics and system monitor capabilities.
17
November ‘16
Electricity+Control