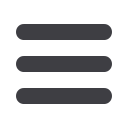

January - February 2015
MODERN QUARRYING
15
AT THE QUARRY FACE
Above:
The ramp is being
shortened to enable more
efficient hauling in terms of the
whole pit, the wall will need to be
shifted towards the east as the
limestone is getting deeper and
deeper.
Centre:
Stacking and reclaiming:
Three are three limestone piles,
one full, one being reclaimed and
one being stacked at 18 000 t
each.
shortages, Diergaardt says the operation is one
of Eskom’s clients on a major drive to save energy,
“and we also switch off some of our equipment
during peak times especially during 18:00 and
20:00 in the evening.”
“We are on Eskom’s time-of-use tariff and in the
mornings between 08:00 and 10:00 we also stop
our plant if our stockpiles are sufficient,” Vorster
confirms, adding that the 18:00 to 20:00 is criti-
cal for Eskom and De Hoek. “We also have a cur-
tailment-of-time contract with Eskom which says
that on request, we will stop operations. So they
will notify us that it’s either a Stage One or Stage
Two, the municipality is load-shedding, and then
at Stage Three, they will ask us to stop significantly
more of our plant.
“If we look at fuel, there is not really much that
we can do. However, despite carbon tax intro-
duction being delayed to 2016, we are busy with
a number of initiatives. In terms of alternative
fuels, we have concluded an agreement with the
Recycling and Economic Development Initiative
of South Africa (REDISA), to process waste tyres at
De Hoek, and to commence the burning of these
by mid-2015. What happens in the landfill areas of
the municipalities and metropolitan areas is that
tyres tend to shift the landfill. You are not allowed
to landfill tyres.
“Some of our competitors are also burning
tyres, but what we are providing is a major capital
outlay to build an automated, environmentally-
friendly facility for this purpose. That is Phase One,
and Phase Two will be refuse-derived fuel from
municipalities in 2018. It’s a process of small steps
to first see the impact from the tyres and then see
the impact from the rawmaterial, and to follow this
up with minor adjustments.”
As part of PPC’s strategy and long-term plan to
grow revenue by 40% outside of South Africa, the
group is expanding its operational footprint into
the rest of Africa, including Algeria, Botswana, DRC,
Ethiopia, Rwanda and Zimbabwe.
Asked where the De Hoek operation fits in, in
terms of PPC’s African strategy, Vorster says: “We
have a slogan ‘Keep the home fires burning’, and
the funding for the African strategy comes from the
group’s South African operations, so we need to be
efficient. De Hoek is a primary plant within the PPC
Group which makes clinker for the Western Cape.”
Products produced at this facility are a 52,5
down to a 42,5 premium cement. “This deposit is
high in alkaline, which assists in making the quality
products at De Hoek,” he adds. “We are very fortu-
nate in having a quality shale and lime deposit.”
There are 48 employees on the quarry side,
21 people per shift, on a two-shift operation five
days a week. “The cement plant runs for 365 days,
on a 24-hour basis, so I have to work smartly for
five days to keep them running for seven days,”
Diergaardt says. Packing and distribution is five to
five and a half days a week. The total staff comple-
ment is 220 people.
“We have quite a few people who have been
with us for close to 30 or over 40 years,” Vorster
tells
MQ
, which is something that says a lot for the
operation.
The picturesque village at De Hoek incorpo-
rates some 75 houses for critical staff, one of whom
is Vincent Diergaardt and his family. The first house
was built in 1921, with the golf club established in
1922. “We love living in a close environment such
as this. It is safe and secure, and we are part of a
wonderful community.”