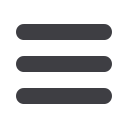

March 2015
MODERN MINING
11
MINING News
www.masterdrilling.com At Master Drilling, passion and excellence are hallmarks of what we do. We tailor-make innovative drilling solutions for our clients that keep up with an ever changing mining environment. Rock boring Raise boring ・ Box hole boring ・ Horizontal raise boring ・ Slot boring ・ Blind shaft boring ・ Tunnel boring ・ Reef production boring Slim drilling Core drilling ・ Percussion drilling ・ Reverse circulation drilling ・ Mud rotary drilling ・ Air rotary drilling Master Drilling is an ISO 9001, ISO 14001 & BS OHSAS 18001 accredited company. Drilling Solutions Specialised GlobalBulk sampling programme
starts at Oena diamond project
Canadian company Tango Mining Limited reports that the bulk
sampling programme at its Oena project in the Northern Cape
began in February on schedule. Oena is located 50 km upstream of
Namdeb’s Auchas and Daberas alluvial diamond mines which are on
the Namibian or north bank of the Orange River, while Trans Hex’s
Reuning and Baken alluvial diamond mines are respectively 15 km
and 60 km downstream of Oena on the South African or southern
bank of the river.
Mining contractor earthmoving equipment to support a 1,5 Mt/a
throughput capacity has been mobilised to the site and the first
24 421 tonnes has been excavated, of which 3 390 run of mine tonnes
have been processed through the newly commissioned rotary plant
and recovery system.
According to Tango, the newly acquired high volume Bourevestnik
(SA) (BVX) X-ray recovery equipment, to be commissioned in March
2015, will allow for increased recovery efficiencies and product insur-
ance and protection.
of 54 PCUs across Tumela mine’s underground operations.”
Prinsloo said the testing process to date had included engage-
ment with the union leadership, underground crews and employees
in general to ensure that all stakeholders were involved in playing a
role in establishing the value of any new interventions undertaken by
Tumela mine. He said the positive feedback and blasting results had
led to this next phase.
“Our resources on site include a PCU workshop, a training centre
and spares stores for the support of operations,” said Albie Visser,
BME’s General Manager for South Africa. “We have 12 staff on site to
ensure a smooth roll-out, including managers, administrators, main-
tenance technicians and training practitioners.”
Among the breakthroughs achieved in the evolution of the PCU
has been its compact, lightweight and robust design; weighing just
14 kg, the pump component is carried separately from multiple
20 kg emulsion bags. The sensitiser tank is also in a separate con-
tainer – latched onto the pump just before charging – and renders the
emulsion ready for blasting as it enters the blast hole.
“Our Closed Emulsion System prevents emulsion contamination
and waste through the use of dedicated bag-filling stations, located
underground close to the work face,”said Pearton.“These stations are
supplied from transfer cassettes which bring the emulsion from our
facilities on surface.”
He said the simplicity of the pump’s design and operation proce-
dures allows training to be conducted cost-effectively and relatively
quickly, with training facilities including a mock-up blasting rig to
ensure real experience during training.
“The quality of BME’s emulsion is another vital element of the
process,” said Pearton, “as it can be pumped numerous times without
causing any product degradation; it can also be stored for extended
periods with no reduction in quality.”
To optimise efficiency and minimise downtime underground at
Tumela mine, units can be easily ‘exchanged’ and replaced from the
stores. Radio frequency identification (RFID) technology is employed
to track the location of pumping units at all times.