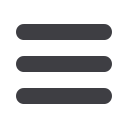

GOLD
22
MODERN MINING
March 2015
The concentrate stream
is subjected to the new
fine-grind process, which
involves milling the slurry
material with tiny beads
using four vertical stirred
mills, three of which are
seen here (photo: Arthur
Tassell).
well as an extensive network of pipelines. The
Brakpan plant is DRDGOLD’s flagship and is
responsible for the majority of production, with
most of its feedstock (roughly two thirds) being
sourced from the Elsburg tailings complex and
the L/29 dump. The overall resource being
exploited by Ergo amounts to 11 Moz of gold.
DRDGOLD has been involved with the Ergo
assets since 2007 (initially in joint venture
with Mintails, whose stake it purchased in two
deals in 2008 and 2010) and has since mod-
ernised and extended the operation, among
other things constructing a 50 km long, 600 000
tonne/month capacity, HDPE-lined pipeline to
link Crown and the Brakpan plant. The FFG
circuit is the latest enhancement of the opera-
tion and is designed to increase the efficiency
of extraction by roughly 0,03 g/t – representing
an approximate 10 % increase in recovery.
The need for the FFG was identified sev-
eral years ago when research by DRDGOLD
(including trials in a pilot plant) revealed
that pyrite particles, containing some 40 %
of the gold entering the Brakpan plant, were
not responding as well as expected to the CIL
process. A dual process solution was identi-
fied – re-introducing flotation (originally used
by Anglo American when the
plant was first commissioned
but subsequently discontinued)
and adding an additional stage
– fine grind or milling of the flo-
tation concentrate followed by
treatment in a small dedicated
CIP circuit. The FFG project was
approved in 2012 and imple-
mented during 2012 and 2013
by DRDGOLD using an in-house
project team.
Although the FFG or high-
grade circuit came on line in
January last year, it operated for
less than three months before
DRDGOLD decided to suspend
the new section – a decision that
Pretorius described as one of the
biggest and most difficult deci-
sions he has had to take since
joining DRDGOLD ten years ago.
“Suspending something that
was brand spanking new was
difficult,” he said. At the time
the decision was announced,
DRDGOLD said that while the
float and milling sections had
performed well, the CIP had not
yet stabilised and appeared to
be contributing to metallurgical
instability and carbon inefficiencies down-
stream in the CIL or low grade section.
By September last year, DRDGOLD had
completed an analysis of the problems and opti-
mised the circuits and was confident enough to
reintroduce one stream of the three-stream FFG
circuit, with generally positive results. It fol-
lowed up in January this year by restarting the
other two streams. Commented Pretorius: “The
plant has its own personality, its own tempo,
but we are now starting to see the upside of the
flotation and fine grind coming through.”
With the FFG now fully operational, all the
slurry entering the Brakpan plant enters the flo-
tation section after passing over linear screens
to remove organic material and debris. After the
material is conditioned with reagents, it enters
the float cells where it is separated into two
streams. One stream, the flotation concentrate,
contains the sulphides which are enriched with
gold while the second stream, the flotation
tails, is made up of lower-grade material which
is treated in a conventional CIL process, which
is the treatment process that has been used for
the past 30 years with an extraction efficiency
of 39 % to 40 %.
The concentrate stream is subjected to the