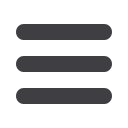

Technology
news
Wire & Cable ASIA – January/February 2012
53
encoder that allows
wire and cable products
product means the plant can generate a
substantial quantity of material scrap or
waste. This can cost manufacturers a
significant amount of money in
unnecessary expense. As such, length
accuracy is of paramount importance.
Non-contact approach eliminates
measurement errors
Non-contact length and speed
measurement systems avoid the
measurement pitfalls encountered by
mechanical contact systems. For
example, the LaserSpeed encoder uses
a unique, laser-based measurement
technique that does not make contact
with the wire or cable. It is permanently
calibrated and has no moving parts to
wear out. The system projects a unique
fringe pattern on the surface of the wire
or cable. As the product moves, this
movement creates a Doppler signal
scattered back to the LaserSpeed
system.
This Doppler information is translated
into product speed and pulses are
produced to determine the product
length. The LaserSpeed encoder works
on all types of products, regardless of
colour, shape or texture. Length and
speed measurements are captured with
better than ±0.05% accuracy and
±0.02% repeatability.
Ensuring marking accuracy during
sequential printing operations
Depending on the production require-
ment, manufacturers have installed the
LaserSpeed encoder at various
locations on the line. The most
common place is adjacent to the
printing system just after the jacket is
extruded onto the wire or cable. Since
the jacket is still soft and hot after the
extrusion, the LaserSpeed non-contact
system provides the ideal measurement
method over contact mechanical
encoders.
Many manufacturers have installed the
LaserSpeed encoder before the
capstan station or take-up reel.
Situating the LaserSpeed encoder
alongside the printing system where the
marking occurs, helps to better track
the actual length and speed.
To control the sequential printing
operation, the LaserSpeed encoder
outputs an index pulse directly to the
printing system. Some applications may
just need the encoder pulses via a
quadrature output. Pulses can also be
sent to a PLC system.
LaserSpeed enables manufacturers to
set the desired pulse rate (ex. pulses
every number of feet, metres, etc.) to
meet their unique sequential printing
requirements.
This enables the manufacturer to
control the exact spacing between print
marks with ±0.05% accuracy. Under
controlled conditions, it is possible for
LaserSpeed to approach ±0.02%
accuracy. This level of accuracy also
ensures the manufacture does not
over-ship or short the customer of
▲
▲
LaserSpeed uses non-contact laser technology to measure product length and speed
with ±0.05% accuracy
product. For European manufacturers,
the LaserSpeed encoder is available
as a MID-certified system to meet all
the Measuring Instrument Directive
requirements.
Setting the pace for accurate length,
speed, and sequential printing
The advantages of non-contact length
and speed measurement systems,
such as the LaserSpeed gauge, have
been proven on all types of wire and
cable production processes including
sequential printing applications.
This non-contact, laser-based tech-
nology eliminates those measurement
errors associated with contact wheel
tachometers as a result of slippage and
mechanical wear.
Manufacturers that employ laser-
based, non-contact measurement
technology in their sequential printing
operations will be on the road to
increased
productivity,
improved
product quality and real bottom-line
savings.
Beta LaserMike – USA
Fax
: +1 937 233 7284
:
sales@betalasermike.comWebsite
:
www.betalasermike.com