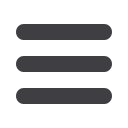

Braiding, knitting, weaving
&
welding
Wire & Cable ASIA – January/February 2012
62
About ten years ago, Maschinenfabrik Niehoff started to
develop the BMV type braiding machines together with
the data and special cable stranding machines of the DSI
series. The 12, 16 and 24-carrier lever arm rotary braiding
machines are mainly designed to apply an EMC shielding
onto cables. At wire 2012 trade fair, another BMV model will
be introduced.
Because of its precise tension control system and the
simplicity of its wire path, the industry proven BMV braiders
can process a multitude of wire material and types eg bare
or plated copper wire, aluminium wire and stainless steel
wire with a single-wire diameter of 0.05 to 0.3mm (44–28
AWG) as well as artificial yarn and fibres.
The machines’ sophisticated design allows the processing
of the different material copper, textile and steel wire braids
without the need of extensive and time consuming setups
and changeovers.
Typical applications of the braiders include the manufacture
of data, control cables, coaxial cables as well as automotive
hybrid drives cables, in which tapes must be inserted before
and after braiding.
Further applications are hollow braids for battery cables,
stranded braids, mechanical reinforcements for pressure
hoses and medical catheters.
The BMV braiders are equipped with the latest technology
energy saving drives, energy optimised components and
new spool carriers made of precision-machined high-grade
aluminium.
The braiders feature an automatic central lubrication
system, an infinitely variable electronic line speed and
braiding pitch control as well as a quality control system
from the cable inlet via single and bundle-wire control to
the take-up of the braided cable. Also an automatic empty
bobbin detection system can be integrated in the
machine: this device stops the machine before
a braiding bobbin is completely empty, while
minimising the residual wire on the braiding
bobbin. The operational safety can still be
increased using slide track temperature monitoring
and control which varies the track lubrication
frequency and quantity to avoid overheating
and which stops the braider when a limit
temperature is exceeded. Thus BMV braiders can
operate unattended and with minimum operator
intervention.
The BMV machines can be combined with either
longitudinal or central taping devices designed to
apply tapes of different materials onto the cable,
before or after the braiding point. Because the
working process is integrated in one machine,
work and storage spaces are reduced requiring
considerably smaller equipment footprints.
Moreover, the product quality is higher than before
because of the elimination of the intermediate
rewinding process and the in-line braiding and
taping operations are completed under constant
and uniform haul-off tension. Therefore, braiding
and subsequent taping of a cable in one step
results in considerable operational advantages and
cost savings.
The BMV braiders are part of the modular Niehoff
machinery programme which covers all operational
steps from rod wire drawing to fine wire drawing
and to data and special cables manufacturing.
The “Hacoba System” bobbin rewinding machines,
also built by Niehoff, play a key role in enabling
the BMV machines to work efficiently at their full
potential.
Maschinenfabrik Niehoff GmbH & Co KG –
Germany
Fax
: +49 9122 977 155
:
info@niehoff.deWebsite
:
www.niehoff.deEfficient and economical Niehoff
braiders: the BMV series
❍
❍
BMV 16-carrier lever arm rotary braiding machine (BMV 16)