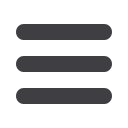

Wire & Cable ASIA – September/October 2007
68
January/February 2012
The document
[2]
specifies a flame propagation test on the
completed cable according to IEC 60332.1.
4.8 Absence of halogens
In the case of fire, acids caused by the smoke of
halogenated materials are a serious danger for people’s
health as well as for the function of electric and
electronic devices.
In former times halogen free cables were required in public
areas such as hospitals, airports and
other similar structures.
But due to the increasing importance
of electronics in all areas of every-
day life, this quality is increasingly
required in industrial premises, too.
As far as for solar cables, this
characteristic is especially important
for solar power devices on residential
buildings.
Several tests have to be performed
to prove the absence of halogens in
solar cables. Electrical conductivity
and pH value of the smoke are to
be quantified according to European
standard EN 50267-2-2.
The content of chlorine and
bromine is determined according
to EN 50267-2-1 and a special test
is developed for the content of
fluorine in Annex C of the discussed
specification
[2]
.
5 UL 4703 Standard
In 2005 the American Underwriters
Laboratories (UL) published the UL
subject 4703 “Photovoltaic Wire”
[3]
.
It covers single conductor, insulated
and integrally or non-integrally jacketed,
sunlight resistant, photovoltaic wire in
several temperature and voltage ratings
for interconnection wiring of grounded
and ungrounded photovoltaic power
systems.
The standard UL 4703 is based on the
service entry cords USE-2 and speci-
fies some additional requirements for
photovoltaic cables.
It applies for solar cables in North
America.
These
UL-requirements
are quite different from the German
specification.
The UL standard leaves more freedom
for the manufacturer as far as the
cable construction and the selection
of materials is concerned. One or
two insulation layers can be chosen
optionally as well as a “skinned” single
layer construction.
For two-layer construction, as specified in the
DKE-document
[2]
, several combinations of wall thick-
nesses are allowed in UL 4703. But in each case the total
sum of wall thickness will be higher than specified in the
German specification (see
Table 1
).
Thus the diameter for the same conductor cross section
will be higher which reduces the suitability for several
connectors. And the increased need of insulation
compound will add to the production cost.
❍
❍
Figure 3
:
Arrangement for penetration test on completed cable
Dimension
AWG 10 – AWG 18
AWG 2 – AWG 9
Single layer
1.52mm/60mils
1.91mm/75mils
Skinned
1.91mm/75mils
(1.14mm + 0.76mm)
2.28mm/90mils
(1.52mm + 0.76mm)
Double layer
2.28mm/90 mils
2.66mm/105mils
(1.14mm + 1.14mm)
(1.52mm + 1.14mm)
Parameter
DKE
[2]
UL 4703
[3]
Cable Type
Solar Cable
Based on RHHW/USE-2
Cold Bend/Cold Impact
-40°C
-40°C
Hot Pressure Test
+140°C
+121°C
Ageing Test
+150°C
+121°C
Humidity Test
1000h/90°C/85% rel.
Not required
Dynamic Penetration
Ambient temp, 150N * √_
Not required
Fire Performance
IEC 60332.1.2
UL 1581 sec. 1060
UL 1581 sec. 1080
UL 1581 sec. 1061
UL 1581 sec. 1100
Halogen Free
EN 50267-2
EN 60684-2
Not required
Weathering/UV-Test
HD 605 S1/A1
UL 1581 sec. 1200
❍
❍
Table 1
:
Wall thicknesses acc. to UL 4703
❍
❍
Table 2
:
German specification versus UL 4703
1 Shoulder with sufficient depth for testing the insulation
2 Needle of spring steel
3 Sample