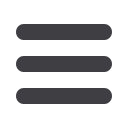

STANDBY + BACK-UP
ROUND UP
Oil control cartridge valves available throughout Africa
As part of the new joint venture into Af-
rica, the Hytec Group has increased its
distribution and support of the full range
of
Bosch Rexroth
Oil Control cartridge
valves throughout sub-SaharanAfrica.This
expanded support will enhance the Group’s
logistical, sales and support capabilities of
the products, and includes amore competi-
tive pricing structure for this series.
The valve range simplifies conventional
compact hydraulic systems, and enhances
hydraulic circuits where space and weight
present fundamental application con-
straints. Bosch Rexroth cartridge valves
are characterised by a very long service
life: at an operating pressure of 350 bar,
the cartridge solenoid valves are rated for
a product life of 10 million cycles.
The unique design of the cartridge valves
reduces the amount of interconnecting
pipework required within the hydraulic
circuit through a customised manifold.
This reduces the overall weight, and space
requirements, of the machine, resulting in
decreased power requirements – contrib-
uting to better all-round energy efficiency.
Because the interconnections of piping
within a conventional hydraulic system
are a common source of fluid leakage,
the compact design and reduced piping
requirements of the cartridge valves also
reduces inspection and maintenance re-
quirements, facilitating a more efficient
hydraulic operation.
Enquiries: Louis Roode. 11 573 5400 or
General purpose globe control valves
Mitech
’s general purpose Globe Control valves
offer superior performance while permitting
easy, fast and inexpensive maintenance. The
standard Mitech Globe control valve can be
used for many applications and offers high po-
sitioning accuracy and tight shut-off together
with compact size and robust construction.
Due to the modular design it can be easily
adapted to satisfy many special requirements
such as high or low temperature, corrosive
duties, three-way configuration and high pres-
sure drop applications.
The valves are available from the standard
type up to the specially designed severe ser-
vice valve in ½” to 24” NB and up to ANSI 4500. The valves may
feature tight shut-off, low noise, cavitation control and energy dis-
sipating trims.The entire Mitech range of control valves utilise the
clamp in place, free floating seat design. All trim components are
designed to clamp in place so the valve can be quickly configured
to the user’s specific process needs.The free float of the seat and
plug during assembly means that stem, plug and seat alignment
is easily achieved.When compared to alternative designs, the free
float design provides the user with longer stem seal life and better
valve shut-off performance.The simplicity of build also means that
maintenance is quick and easy, with no special tools required to
achieve the design performance of the valve.
Enquiries: Pieter Badenhorst.Tel. 011 927-4850
or email
enquiries@mitech.co.zaPressure testing of Koeberg's containment building
Recognised as
Eskom
’s most consistent
and reliable power station, Koeberg is
the only nuclear power station in Africa.
Koeberg has a pressurised water reac-
tor design. Featuring the largest turbine
generators in the Southern Hemisphere,
Koeberg is also themost southerly-situated
nuclear power station in the world. With
International Law stipulating that all con-
tainment buildings of all nuclear plants
have to be pressure tested every ten years,
Eskom contracted Rand-Air to facilitate the
assignment.
The purpose of the pressure testing of
the containment building at Koeberg was
to ensure that there was no leakage which
could be harmful to the surrounding envi-
ronment and public.
Using ten PTS916 Rand-Air units running
through desiccant dryers, dry oil-free air
was pumped into the containment build-
ing. Both the inner and the outer sector of
the building were surveyed before, during
and after the test.Water particles have a big
influence on pressure testing and the end
result. We were required to match 18 °C in
temperature of the air going into contain-
ment. Heat exchangers and chillers reduce
the pressure testing time by a few hours
allowing for control of the air pressure dis-
tribution.The requirement for the pressure
testing was minus 20 °dew point - minus
40 was achieved.
The pressure test took between seven to
eight hours. It took two and a half hours to
reach a pressure of one bar.The procedure
stops for eight hours when it reaches one
bar, this is key in ensuring that everything
is stable enough to continue to four bar.
The process requires the go ahead from
two parties namely Électricité de France
(EDF) and Eskom. It is critical to monitor
the progression thoroughly as damage to
the equipment inside the building could be
detrimental. The pressure test at Koeberg
was a success.
Enquiries: Visist
www.eskom.co.zaVALVES + ACTUATORS
Electricity+Control
July ‘15
40