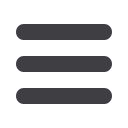

News
Technology
January 2016
49
www.read-eurowire.comThe PWC-S system performs wire
cleaning and polishing in-line with wire
drawing machine at 6 to 12m/s (1,200
to 2,400ft/min). Exceptional cleanliness
permits wire direct brass coating,
copper coating, galvanising and wire
cleaning prior to heat treatment and
coating applications including patenting,
annealing, painting, plastic coating, etc.
The system incorporates new technology
that enables normal cold plant water
to be converted into a unique cleaning
medium
generating
high
pressure
wetting/contaminants extreme pressure
extrusion/hydrodynamic
cavitations
displace, and contaminants flush out,
used to clean drawn wire at high-speed in
a completely green application, providing
a glossy wire finish in plating quality.
The PWC-S system effectively removes
lubricant residue from the base material and
is particularly recommended for cleaning
applications with wires drawn upon severe
conditions resulting in increased heat and
burned lubricant tightly bound to the wire
surface and embedded inmicro-cavities.
For decorative mirror reflective wire
applications, the system can be used
with an emulsion including a new rust
preventive additive diluted at 3-5 per
cent concentration. The PWC-S unit is
compact and can be easily installed on
the finishing/last block of a wire drawing
machine.
Decalub – France
Website
:
www.decalub.comFrom drawn dull to wire clean reflective finish
in plating quality
▲
▲
Wire cleaning by PWC-S system
Collaboration with a Swedish high-tech
cable manufacturer has led Subec to the
development of a new multi-dimensional
Precision
Guide
Unit (PGU). It aligns
and stabilises the
wire in x-y-planes
before
entering
the extrusion head.
This
allows
for
precise
centring
which is especially
needed for fixed
position extrusion
heads.
On the large end of
the guiding range
for big diameter cables and umbilicals,
Subec has won several contracts with
Swedish and Norwegian HVC plants. A
constant high quality of guide rollers
made of polyurethane coated steel make
sure cables are not damaged during
transport to the waterfronts at the Baltic
Sea and Norwegian Sea.
Subec AB – Sweden
Website
:
www.subec.seDeveloping new
guiding solutions
▲
▲
Subec's new multi-
dimensional Precision
Guide