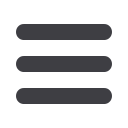

I
ndustry
N
ews
www.read-tpt.comM
ay
2010
37
›
THE MOST ADVANCED MFL TECHNOLOGY AVAILABLE
Scan Systems Corp Houston, Texas USA +011.281.219.9480
www.PitcoInc.comDIGI-TECH™ M-Series
MFL Pipe Inspection Unit
PITCO
A DIVISION OF SCAN SYSTEMS CORP
BEST IN CLASS
OCTG MFL
TUBING AND CASING
INSPECTION SYSTEM
• Full Body Inspection
• MFL Longitudinal Inspection
• MFL Transverse Inspection
• MFL Magnetic Flux Density Wall Thickness Inspection
• Eddy Current Grade Comparator
• Better Sensitivity with Hall Elements Detector Sensor
• Fully Digitized at the Signal Detector for Reduced Noise
• Effective up to 0.625” (15.875mm) wall thickness
• Production Speeds up to 150 FPM (0.75mps)
• Fully Computerized and Controlled Systems
• Industry-leading Digi-Pro
TM
Signal Processing Electronics
• Equipment Sizes for 1 ½” (38mm) through 14” (356mm)
PRICE PERFORMANCE VALUE
FRIEDRICH Kocks, Germany, has received
an order to supply a stretch reducing
block and a rotating hot saw, for the core
of a new continuous production plant.
The order was placed by China National
Petroleum Corporation within the frame of
the construction of a welding tube plant at
its subsidiary Baoji Petroleum Steel Pipe Co
Ltd in Baoji, China.
Baoji Petroleum Steel Pipe was originally
founded in 1958, and was the first Chinese
manufacturer of tubes using the submerged
arc welding method. The company now
produces 1.25mn tons of steel tubes per
year in several works. Its new welding tube
plant has been designed to allow continuous
welding and stretch reducing in one step –
the tube is in the welding line and in the
stretch reducing block at the same time.
After completion, the new plant will
produce up to 300,000t/a of high-quality
welded tubes. The range of products will
include tubes within a diameter range of
60.3 to 177.8mm, with wall thicknesses of
4.83 to 13.72mm, according to international
standards for applications in the oil and gas
industry. The 3-roll stretch reducing block in
‘star drive’ design, which will be
used for the first time in a tube
welding plant, will roll all finished
sizes out of only one mother size
of 193.7mm diameter.
The SRB will be designed for
theuseofupto24non-adjustable
and adjustable stands with a
nominal roll diameter of 360mm.
The last three stands used in the
block are adjustable finishing
stands; the other stands are
non-adjustable reducing stands.
The quick changing system for the stands
and the roll shop with quick roll changing
reduce the required quantity of changing
stands, for optimum production.
The RHS 1000 rotating hot saw, which
will be installed between the SRB and the
cooling bed, allows the production of different
tube lengths with tight length tolerances.
Complicated batch conveyors and saws
behind the cooling bed can be omitted,
reducing investment and maintenance
costs.
The scope of supply also includes roll
shop equipment, electrical equipment,
automation systems, and basic engineering
for local production (obligatory in China),
such as gratings, roller conveyors, ejector
and cooling bed. Supervision of assembly
and commissioning, training of operators,
and the transmission of process know-how
are also Kocks’ responsibility.
Commissioning of the new tube mill is
planned for the second half of 2011.
Friedrich Kocks GmbH & Co KG
– Germany
Fax: +49 2103 54 028
Email:
v.d.heiden@kocks.deWebsite:
www.kocks.deGerman equipment installed at Chinese tube plant
The machinery produces tubes up to a diameter of 177.7mm