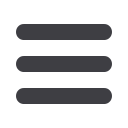

T
echnology
U
pdate
42
M
ay
2010
www.read-tpt.com›
Metalloobrabotka Moskau 2010
Hall 2.2 / Booth B10
Modular
Machine Tools
www.unitube.defor the machining of ends
of workpieces
Premium Joints
Cutting off
The smaller blade diameter with higher
blade stiffness used by the Linsinger Multi-
Cut MC3 offers the bonus of significantly
improved blade life. The resulting
additional savings in running cost reduce
the pay-back period to two to three years
over conventional large blade sawing
machines.
As Hans Knoll, Linsinger CEO
commented: “The Multi-Cut is a very low
LINSINGER Multi-Cut features three
small diameter circular saws mounted on
a rotating frame. The tube is positioned
and clamped and the three circular saws
cut into the tube while the frame rotates
120°. The very short cycle times enhance
the output performance of state-of-the-art
tube mills.
The robustly designed control system
allows independent operation of each
saw blade, and enables uninterrupted
production, even in the event of partial tool
breakage. This feature reduces unplanned
stoppages by automatically allowing
production to continue without interruption
with two saw blades and the frame rotating
240°.
The lifetime renewal cost of conventional
large diameter blades is many times higher
than the initial machine investment. The
potential savings offered by the smaller
Linsinger Multi-Cut blades far outweigh
the additional machine investment. For
example, for tube diameter range 150–
660mm, the renewal cost of a Multi-Cut
blade is up to 15 times lower than the
renewal cost of a conventional large
diameter blade.
cost solution. Even if others would give
away conventional sawing machines
for free, the potential operating savings
offered by the Linsinger Multi-Cut prove to
be more attractive. Multi-Cut technology
is not only cheap to operate, but also well
proven, having been derived from flying
tube cut-off know-how.”
Linsinger Maschinenbau GmbH
– Austria
Fax: +43 7613 8840 951
Email:
maschinenbau@linsinger.comWebsite:
www.linsinger.comMulti-Cut MC3 tube cut-off machine
Combination for thread generation
TOOLING giant Walter GB is offering the
twin force combination of Titex drilling and
Prototyp tapping as a tooling package for
high-performance yet cost-effective thread
generation.
The Walter Titex X-Treme Plus drill
provides effective machining of up to five
times diameter on steel, cast iron, stainless
and non-ferrous materials courtesy of an
internal coolant supply coupled with Walter
Titex’s innovative double performance line
(DPL) double coating.
Comprising a basic coating to protect
the tool and to optimise the adhesion of
the special tip coating, the innovative DPL
technology enables the tool to operate at
greater cutting speeds than usual while
offering extended tool life at conventional
cutting parameters.
Complemented by any one of three
Walter Prototyp taps, the result is maximum
thread generation efficiency. The trio is:
Prototyp ECO-HT tap – a universal HSS-
E-PM tap with THL coating and innovative
surface treatment, capable of operation at
three times diameter for use in both short
and long chipping materials, and offering
high-integrity process reliability without
bird nesting and with long tool life even at
maximum cutting speeds; Prototex ECO-
HT – with spiral point form for through-hole
thread generation; Paradur ECO-HT – with
R45 helix angle, chamfer form C, bevelled
thread run-out and long flutes for blind
hole threading.
Walter GB is providing the ‘off-the-shelf’
kits for blind and through-holes – each
equipped with a Titex X-Treme Plus drill
and two Prototyp taps – in a range of sizes
to suit varying applications.
Walter GB Limited
– UK
Fax: +44 1527 839499
Website:
www.walter-tools.comThe Linsinger Muti-Cut