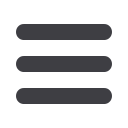

M
ay
2010
77
›
T
echnology
U
pdate
Worldwide, 2 out of 3 end users are equipped
with Polysoude welding technology. Discover the
widest range of orbital weld heads and power
sources for tube, pipe and tube-sheet welding.
State of the art – field proven solutions, easy to
handle for outstanding quality and productivity.
Orbital Welding
SOlutiOnS
extremely
reliable
POLYSOUDE
2, rue Paul Beaupère - 44300 Nantes - FRANCE
info@polysoude.comTel.+33 (0) 2 40 68 11 00 - Fax +33 (0) 2 40 68 11 88
www.polysoude.com50 Years of Excellence in Providing
Innovative Weld Technology
and Expertise.
Worldwide Organisation Provides
Support Next to You.
International Sales and Service,
On-Site Training and Maintenance
with Rental Options.
THE ART OF WELDING
- 10120
Gb_SoudageOrbital_87X262.indd
113/01/10 14:58
MM1 computer-controlled
pipe cutting machine
THE MM1 is a computer-controlled machine that automates the
cutting of profiles, holes and shapes on pipe with diameters from
10 to 40cm (4" to 16"). It rotates the pipe on its roller bed with
a three-jaw chuck, while simultaneously moving a cutting torch
back and forth along the pipe’s axis.
Pre-programmed shapes such as saddle, hillside, lateral
and mitre cuts can be made by simply selecting the type of cut
from the menu, then entering the diameters of the pipe being
processed and pressing the run button. Templates are not
required, and there is no time-consuming layout or calculation.
Irregular or uncommon shapes can be plotted, programmed and
saved for future use.
The machine’s pipe bed is designed for handling lengths of
pipe up to 1.83m (6ft). Additional pipe bed extensions of 2.44m
(8ft) can be added to make a bed of up to 11.6m (38ft).
The method of cutting can be oxy-fuel or plasma. If oxy-fuel
is used, the machine will be equipped with solenoids and a
three-hose cutting torch. When plasma is used, a rotary ground
is installed on the machine. The machine can be delivered with
plasma torch leads and power source, or the customer may
provide their own plasma equipment.
Cypress Welding Equipment Inc
– USA
Fax: +1 412 331 0383
Email:
jwhite@weld.comWebsite:
www.cypressweld.comTube end conditioning
machine from the UK
AS part of its ongoing innovation programme, Nuke Tool
has announced the introduction of the Sidewinder tube end
conditioning machine.
The Sidewinder is a machine dedicated to the power
and process industry, and especially to those involved in
the manufacture and repair of boilers, shell and tube heat
exchangers, condensers, economisers, element and membrane
wall panels.
In operation, the Sidewinder pilots within the bore of the tube
while its powerful conditioning motor orbits the outside diameter,
carrying out the cleaning/polishing process. Tube sizes from
19 to 88.9mm (0.75" to 3.5") can be handled, and the whole
procedure is carried out in seconds.
The Sidewinder is a pneumatically operated unit (electric
drive option available), and supplied in a double walled, injection
moulded case, complete with low speed pneumatic drive
motor, choice of three pilots, and a choice of three conditioning
heads.
Nuke Tool Ltd
– UK
Fax: +44 1782 316200
Email:
info@nuketool.co.ukWebsite:
www.nuketool.co.uk