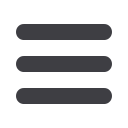

provide strong support; however, new
instruments typically require much less
support than older equipment. The need
for support increases as instruments
age, but an OEM’s support capabilities
typically decline due to discontinuance
of manufacturing, reduced parts supply
and fading expertise (Figure 1).
The underlying cause is the natural
lifecycle of any commercial product:
introduction, growth, maturity and
decline (Figure 2). Every product
progresses at a different rate, driven by
outside factors: adoption by customers,
competition from other manufacturers,
overall economic conditions, and so
on. As demand declines, OEMs often
introduce new products to replace
aging models, and this requires new
investments in manufacturing, parts
and expertise.
As each product ages, the OEM
makes tradeoffs and decisions about
the allocation of the scarce resources
dedicated to manufacturing and
support. Sustaining an older product
consumes resources that could be used
to develop new products based on
newer technologies (Figure 3).
One reason to shift resources is the
expectation of higher returns on the
money invested in a new product.
Astute OEMs do this in a manner that
meets the needs of existing customers
by providing compatibility modes,
over into a gradual decline, the next
generation of OEM products is in the
growth phase (refer back to Figure 3).
Parts availability is the other major
factor. An instrument, such as a
microwave signal analyzer, contains
thousands of individual parts produced
by hundreds of vendors. Each part
goes through its own lifecycle, from
introduction to discontinuance. External
forces such as changes in government
regulations (e.g., RoHS compliance)
may also affect parts availability.
Parts manufacturers, as independent
businesses, also go through a natural
lifecycle of growth and decline.
Extending the Life of a Test
System
All of the preceding provides context
- but it is still possible to create an
effective strategy that adds years to the
usable life of a test system. The best
chance to plan and execute this strategy
is at the time of the original purchase.
If this opportunity has passed, there is
still time while the instruments remain
in production. Even if the instruments
are out of production, there are ways
to extend system life.
At the initial purchase (Warranty Period)
As noted above, A/D systems may be
expected to last 15 years or longer.
When defining a test system and
evaluating the available instruments,
Figure 1. Instrument Lifecycle
Solutions address service
requirements for the instruments
customer’s use to support long-
term programs
long lead times for notification of
discontinuance, and extended service
capabilities.
The most challenging scenario is an
aerospace/defense (A/D) program,
which may be expected to live for 15
to 25 years. In general, the duration
of a commercial product’s lifecycle
is much shorter than that of an A/D
program (Figure 4). This creates a
timing problem: in many cases, the
instruments in a test system have
passed their peak demand and are
beginning to decline as the A/D
program is reaching its peak. As the
A/D program crests and then noses
Figure 2. There is often an out-of-phase
relationship between an OEM’s ability to
provide support and a long-term program’s
need for that support
Figure 3. The traditional product-support lifecycle
periods (bottom bar) follow the demand lifecycle
(red curve)
36 l New-Tech Magazine Europe