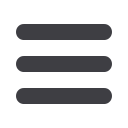

⎪
Pump systems, pipes, valves and seals
⎪
Mechanical Technology — June 2015
13
“
I
have heard, time after time,
that someone was in desperate
trouble because a pump wasn’t
working properly. That’s right!
The darn pump just doesn’t work as it
is supposed to. My response is always
the same: I go there and find out why
the pump isn’t working as designed.
Sometimes it is true that the pump didn’t
perform as designed, but rarely is it be-
cause of a faulty pump,” says Densmore.
Following a request from The Pump
Guy, Larry Bachus, Densmore visited
a town called Daggett, California (just
outside Barstow), where the engineer-
ing department of a large cogen solar
company had asked him to help with
a problematic pump. “I called the
company and spoke by conference
call with Phil Jones and a battery of
engineers. They were convinced that
something had happened to a critical
pump at the solar plant. They needed
someone to determine what should be
done. We agreed on a fee and two days
later, I drove to the job site in Daggett,
California,” he relates.
“The site engineers first escorted me
to the conference room. It was apparent
they were anxious to get this pump into
production as soon as possible. They
were willing to do whatever was neces-
sary to fix the pump. Then, we went to
see the pump.”
The pump had been in service for
25 years, pumping thermal (very hot)
oil. The oil temperature varies between
93 and 232 °C, depending on the time
of day and the amount of sunshine. The
pumps would then push the thermal oil to
a generation facility to produce electricity.
The pump was a Byron Jackson,
heavy-duty single-stage pump with
500 mm suction and discharge ports,
both located vertically at the top of the
pump. It was one of three pumps that
operated in parallel, when required, to
meet the flow requirements. The three
pumps and the piping were coated with
thick insulation to handle thermal oil
that was being circulated from the solar
panels. But the problematic pump was
While waiting for a flight from Joburg’s OR Tambo Airport, Pump Guy, Larry Bachus
receives an email that asks “When is a pump problem not a pump problem?”, along with
the answer, “When it is a pipe problem!” This prompts him to relate the experience of a
friend, Don Densmore, about an urgent pump problem on a thermal oil application at a
solar power plant in California.
The Pump Guy
When is a pump problem not a pump problem?
piped in a different configuration than
the others.
“I noticed the inlet piping was installed
in a manner that could not be considered
‘good engineering’. However, it had been
operating like that for 25-years. With
that in mind, I asked for the pump to be
started to allow me to gather information
from the instrumentation to determine
what was going on.
“As the speed was ramped up from
the VFD, I could see the pressure on the
pump inlet was not as high as it was
designed to be. This was a problem. And
the inlet pressure began dropping steadily
as the speed increased. This indicated an
obstruction. I could also hear the pump
was definitely suffering cavitation and not
pumping as it should. We let the pump
run for a couple of minutes and then shut
it down. The local managers wanted to
remove the pump and get it repaired,”
Densmore says.
The pump was fed from a manifold
located about 30 m away and positioned
about 3.0 m below the pump base. The
pipe leading to the pump had numerous
elbows with inclines and declines leading
to a 500 mm gate valve and the pump
suction nozzle. There was no discernible
logic to the suction pipe arrangement.
“We cut a small hole in the insula-
tion to reach the pipe wall and installed
a pressure gauge at the exit pipe on the
upstream manifold. We installed another
gauge at the gate valve just before the
pump suction nozzle. We started the
pump again, and noticed a large dif-
ference between the two gauges,” he
continues.
The elevation differential across the
pipe system could explain 10 to 15 kPa
of pressure drop between the gauges. The
numerous 90° suction elbows accounted
for another 15 to 20 kPa pressure drop.
But there was nothing to explain the
240 kPa pressure drop across the suction
pipe system.
“We installed some more strategic
pressure gauges in the suction pipe
system to track the pressure drop. We
determined the major pressure drop was
in the vicinity of the suction gate valve,
which was totally open.
“We removed the thick pipe insula-
tion before the suction gate. There was
a hidden ‘Y-strainer’ at the entrance to
the suction gate valve. No one knew it
was there. The strainer didn’t appear
on the original engineering drawings.
Its existence was completely masked
by thick pipe insulation that was many
years old. After 25-years, the strainer
basket was completely full of sludge
and oil clots, which were backing up
into the suction pipe before the strainer,”
Densmore explains.
The clots and sludge would settle to
the bottom of the pipe before the strainer
when the pump was not running. Then
on starting the pump, the sludge would
lodge into the dirty strainer basket. This
was the reason the pressure continued
declining as the pump speed increased
on start-up.
“At first, I recommended they remove
the strainer from the pipe. But there was
no time to build a spacer pipe or spool to
replace the strainer in the suction pipe
scheme. So, I recommended they leave
the strainer in the pipe, but without
the basket. Besides, there were known
strainers in other parts of the pipe system
to capture and remove clots and sludge.”
The client started the pump. The suc-
tion pressure was adequate with respect
to its margin above the NPSHr. “As I
drove home, the pump was running like
new. The vibrations, cavitation and stress
had disappeared,” he reveals.
“In all my years of solving problems
with pump systems, I find that almost
70% of the pump problems are not really
pump problems but system problems.
The pipe system being worked with must,
therefore, be understood and, to do so,
one should always have a gauge on the
suction side as well as on the discharge
side of the pump,” advises Densmore.
Larry Bachus’ next seminar trip
to South Africa is planned for late
October this year. Contact Phindi or Tiny
(phindi@2kg.co.za, tiny@2kg.co.za) at
2KG Training to register.
q