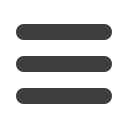

8
Mechanical Technology — January 2016
⎪
Special report
⎪
F
ounded in 1966 in the heart
of the chrome- and coal-rich
Mpumalanga province of South
Africa, Columbus Stainless is
Africa’s only producer of stainless steel
flat products and one of the few inland
stainless steel plants in the world not
connected to a major waterway. “This
site was built in close proximity to
chrome resources and low-cost power,”
begins Matthews. “While this disadvan-
tages us with respect to the logistics of
getting finished product out, we have
easy access to raw materials and we can
run on very low raw material stocks,”
he says.
Today, global stainless specialist,
Acerinox holds a 76% shareholding in
Columbus Stainless with the balance
(24%) being held by South Africa’s
Industrial Development Corporation
(IDC). “Our plant is a technologically
advanced, fully integrated, single-site
operation. This gives us flexibility to ad-
just quickly to changes in the market,”
Matthews points out.
At the starting point of the stainless
steelmaking process is stainless scrap.
“Stainless is the greenest of materi-
als, with 78% being recycled at
the end of a stainless product’s
life,” Matthews says. “In our
process, we melt scrap,
then add some chrome,
nickel and other metals,
according to the alloy recipe
being made. Eventually,
this is converted into sheets
and strips that are stamped,
pressed and welded to make
a host of different products:
for hygienic preparation surfaces
and storage systems; utensils and
containers for almost everything that we
eat or drink; stainless steel components
in critical areas of motor vehicles, such
as exhausts, airbag gas cylinders and
catalytic converters; and for decoration,
signage, shop fittings, architecture, fur-
niture, appliances and modern technolo-
gies such as hydrogen fuel cells.
“Goods manufactured in
stainless steel have a life
of 15 years or longer.
Then, after this time,
the steel comes back
into the plant for re-
processing into new
sheets – and there
is no limit to the
number of times
this can be done,”
he reveals, adding
that this is not just
hearsay: the lifecycle of
stainless steel has been
well documented through
studies at Yale University, for
example.
Stainless steel scrap is a high
value commodity for all stainless
MechTech
takes a tour of South Africa’s
Columbus Stainless plant in Middelburg
and talks to Lucien Matthews (right), the
company’s CEO.
At the heart of the 100 t electric arc furnace
(EAF) is a sophisticated in-house-developed
control system, which delivers composi-
tional control that is among the best in the
Acerinox Group.
Columbus Stainless: A plant tour
manufacturers and, while Columbus uses
as much as possible from local sources,
significant quantities of stainless steel
scrap is imported because there is not
enough in South Africa. “We also make
stainless steel by melting carbon steel
scrap – sourced from within SA – and
then blending that with chrome and
nickel as required,” Matthews adds.
Scrap and ferrochrome
Stainless and carbon steel scrap is accu-
rately sorted into grades in the stockyard,
where overhead cranes – connected to
the company’s in-house order manage-
ment and material flow software system
– weigh and load the required grades into
baskets for delivery to the 100 t electric
arc furnace (EAF).
At the same time, hot molten fer-
rochrome (charge chrome) is trans-
ferred from Samancor’s Middelburg
A basket of raw materials ready to be
loaded into the electric arc furnace
for melting.