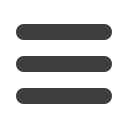

Mechanical Technology — January 2016
9
⎪
Special report
⎪
Left:
Following reheating to between 1 100 and 1 300°C, depending on the stainless steel grade, the slabs
are rolled on a reversing four-high mill to gauges of between 65 and 25 mm.
Above:
Cold rolling of the
No. 1 coils takes place on one of four Sendzimer mills (Z-mills), which produce smooth, shiny finished,
cold rolled stainless steel. The thickness range of the cold rolled product is between 0.2 mm and 6.0 mm.
Below:
The rolled material is then annealed (softened), pickled and passivated, before it is processed
through the skinpass mill, to ensure a smooth surface, known as a 2B finish.
Ferrochrome plant next door, according
to the needs of the stainless steel melt
being processed. This significantly
reduces the logistics costs for both par-
ties and, directly linked to Columbus’
EAF furnace control system, improves
compositional control. The just-in-time
approach also reduces the amount of
post-processing required at Samancor
– to solidify and crush the Ferrochrome
– and the melting energy required per
batch of stainless.
Melting
To make ferritic stainless steels, es-
sentially, only iron and chromium are
needed, but for austenitic stainless
steels, nickel is added to the mix. “Our
compositional control is among the best
in the Acerinox Group,” says Matthews,
“and we are also able to switch between
different material grades several times
per day, giving us a flexibility to respond
to urgent or special requirements from
anywhere in the world,” he adds.
From the EAF, the molten metal is
transferred to one of two 100 t Argon-
Oxygen Decarburisers (AODs). There, by
blowing oxygen, argon and nitrogen into
the molten steel, the stainless steel is
refined. Oxygen decarburises the steel,
but this process is exothermic, which
increases the melt’s temperature. Argon
and/or nitrogen are bubbled through the
mix to accurately control the tempera-
ture and to optimise the decarburisation
process.
Reducing agents, such as silicon and
aluminium, are added to recover some of