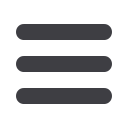

10
Mechanical Technology — April 2015
⎪
Power transmission, bearings, bushes and seals
⎪
A
s a worldwide leader in pow-
er transmission and control,
Bonfiglioli is committed to
achieving the highest ethi-
cal and quality standards, standards
that are documented in the company’s
Bonfiglioli Quality Management System
(QMS). Bonfiglioli is “committed to
designing, manufacturing and supplying
effective products and services that set
a benchmark in the industry. Based on
defined procedures and instructions, the
Bonfiglioli QMS has been established,
not only to ensure the ongoing quality
of our products and processes, but also
to guarantee continuous improvement”,
reads the introduction to the Group’s
quality document.
Historically in South Africa, Bonfi
glioli’s local assembly facility has oper-
ated according the ISO 9001: 2008
certification of the global group. “But
in order to manage the exigencies of
supplying top-quality geared drives to
southern African industry, a fully sup-
ported and functional quality manage-
ment system is an absolutely necessity,”
says Robert Rohman, managing director
of Bonfiglioli SA.
Hence, following local ISO 9001
accreditation by TÜV Rheinland in late
2013, John Beukman was appointed
as the company’s national quality as-
surance manager in November last year.
“We needed to invest in local resources
to better implement the global Bonfiglioli
management system as well as to man-
age our locally accredited ISO 9001qual-
ity system,” Rohman adds.
Beukman qualified as Level 1 Inspec
tor at the Southern African Institute of
Welding before joining IQS (Inspection
and Quality Services), the third party in-
spection specialist. “While with IQS, I was
contracted by a construction company to
oversee the quality control of the auxiliary
cooling systems for the Medupi Power
Station project,” he tells
MechTech
.
Having recently returned from training
in Italy on the Bonfiglioli QMS, he says
that the company’s global quality system
is linked to its SAP enterprise resource
planning system. “Everything from com-
ponent non-conformances to customer
complaints and warranty claims, from
anywhere in the world, is captured by
the SAP system. So all information re-
lating to product or service failures from
branches scattered all over the world,
including internal and customer reports,
can be fed back, collated and analysed
by the group’s global system,” Beukman
explains.
“The underpinning idea is that of
continual improvement,” he continues.
“By sharing information from across the
globe, analysing it and feeding it back
to management and research and de-
velopment teams, the company’s service
offering and its product reliability and
performance can be continuously im-
proved to better meet customer expecta-
tions. The ultimate aim is to become the
preferred partner for industrial drives, by
designing, developing and manufacturing
innovative products that set global quality
benchmarks – regardless of where we are
in the world,” he says.
Bonfiglioli’s Quality Management
System is implemented at three levels:
corporate level, cascading down to the
industrial level and then down to indi-
vidual plant and business units. QMS
procedures have been designed to filter
down from the top, and to then feed
information from the ground all the way
back up to corporate level. “My role is to
implement procedures at plant, branch
and business unit level and to manage
local quality system implementation,” he
informs
MechTech
.
“An enormous amount of research
goes into the development of a new
gearbox and significant amounts of time,
money and effort is spent ensuring that
the quality embedded in the design is
A local quest for quality geared drives
Following local ISO 9001: 2008 accreditation of
Bonfiglioli South Africa’s reducer assembly facility
in Linbro Park, Johannesburg,
MechTech
talks to
John Beukman (left), Bonfiglioli South Africa’s newly
appointed national quality assurance manager, about
the importance and value of complying with global
quality management systems.
transferred, through component manu-
facture and all the way down to local
assembly operations. The last thing the
OEM can afford is to lose the benefits
of a quality design through inadequate
management of the local assembly pro-
cesses,” Beukman notes.
All local Bonfiglioli branches are ,
therefore, under pressure from corpo-
rate to meet global standards in the
final product. “And this is where the
SAP-linked analysis processes kick in.
Any local problem encountered during
a quality test, during commissioning or
a later failure in the field is fed back for
analysis. And we are also subjected to
yearly quality audits from Italy to ensure
that every Bonfiglioli outlet in the world
is performing to the global benchmark,”
he confirms.
Pressure to comply with ISO 9001
quality standards is also being applied
by Bonfiglioli’s local customer base. “We
are operating in a much more regulated
and demanding local market with cus-
tomer that insist that suppliers adhere
to globally accredited quality standards.
Nowadays, potential clients want to look
at a local manufacturing or assembly
facility and inspect its quality credentials
and management systems before they
will even consider using that company
as a supplier. This increasingly applies
to South African mining and project
houses, for example, which need to vet
a suppliers quality systems before grant-
ing approved-vendor status,” Beukman
explains, adding that suppliers who don’t
comply, “don’t get onto the playing field”.