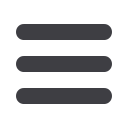

Mechanical Technology — April 2015
5
⎪
On the cover
⎪
BMG company overview
B
MG, which currently generates about
R4-billion of the Invicta Group’s
R10,5-billion revenue per year, is
strategically positioned to service all sectors
of business, including agriculture, mining,
steel processing, robotics, sugar, paper and
general engineering, as well as the automo-
tive sector.
The company, which has grown dra-
matically from a single Bearing Man shop
established in Durban in 1974, now has
over 140 outlets throughout Southern Africa
and continues to expand on the continent.
BMG has become Africa’s leading distribu-
tor of bearings, seals, power transmission
components, electric and geared motors,
as well as belting, fasteners, filtration and
hydraulics. An important area of growth is
in the tools and equipment sector.
BMG boasts 10 specialist divisions, with
advanced technical skills to support the
company’s commitment to applying techni-
cal knowledge and depth of experience to
maximise the efficiency and profitability for
every customer.
Diverse industries can now access
critical production efficiency products and
services from one reliable supplier – BMG.
This integrated approach means that lower
production costs and higher production ef-
ficiencies are within reach of South African
industry, which is desperately in need of
distinct competitive advantages.
BMG’s critical focus is on entire produc-
tion processes. An extensive range of quality
branded components is supported by engi-
neering solutions and technical services to
optimise productivity and enhance process
plant operating reliability.
BMG’s B-BBEE strategy, which is aligned
to the organisation’s strategic objectives,
has been pivotal to the expansion and
improvement of business performance and
operations. The company now has Level 3
certification, with recognition as a ‘value
adding supplier’ (VAS).
q
BMG’s expanded facility includes
specialist assembly and repair
workshops for drives, conveyors,
hydraulics and pneumatics, as
well as electric motors, electron-
ics, gaskets, lubrication systems and
filtration.
Left:
Application of lubrication
on a Tsubaki backstop.
Above:
A Tsubaki
backstop component is being assembled.
the initial design concept and running
through the specification, manufacturing,
quality control, commissioning and after
care of the equipment in use, technical
resources partners each customer to
ensure dependable solutions.
Services include technical applica-
tions consulting, product and system
design, on-site process analysis, lab and
on-site oil analysis, product quality con-
trol and assurance, as well as condition
monitoring services.
BMG World will also be home to field
services. BMG now has 140 mobile tech-
nicians with specialist technical skills and
equipment to conduct breakdown and
routine maintenance on plant. This team
carries out troubleshooting and advises
on possible productivity improvements,
to ensure the highest levels of plant
output and reliability.
Specialist services include instal-
lation, adjustment, replacement and
maintenance of components, shaft and
pulley alignment, balancing, condition
monitoring, oil sampling and analysis
and critical equipment inspections and
lubrication schedules. Maintenance
training and fault diagnosis also form an
important part of BMG’s field services.
The upgraded premises will also
include significantly expanded training
facilities for the Training Academy’s
practical and theoretical training, to take
advantage of MerSETA accreditation for
skills development and training. This
will be open to both company employ-
ees as well as BMG customers. The
company is in the process of expanding
the scope of its SAQA-aligned training
modules and recognises the need to
grow engineering skills, not only for its
own succession requirements, but also
for the development and sustainability
of African economies.
BMG’s internationally recognised
quality management systems endorse
the meticulous standards and proce-
dures that have been developed and
entrenched throughout
the Group. Quality is of
paramount importance
and the procedures and
instructions that have been
developed and entrenched
ensure the quality of all
products and services
meet local and global
specifications and
exceed customers’
expectations.
Accreditations
include ISO 9001
2008, as well as
functional compli-
ance with ISO 18001
OHSAS (occupational
health and safety) and
ISO 14001 (environmental).
ICT operating systems include an
integrated ERP system, a warehouse
management system and an inventory
optimisation system.
BMG is committed to providing
24-hour customer process support for
production efficiency and reliability-
centred maintenance. This is enhanced
by advanced technical and design sup-
port across all functional disciplines.
q