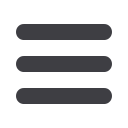

April - May 2016
MODERN QUARRYING
15
SAND PROCESSING
AT THE
QUARRY FACE
deposit is located close to the water table
and Gilbert says that as the valley gets
muddy and “very clayey,” the sand recov-
ery rates for the operation become more
problematic.
“It’s basically a river deposit and it is
quite deep,” Gilbert explains. “We usually
wait until November before we start oper-
ating because the river level goes down
and that means the ground water across
the region drops.”
Mawsons has employed earthmoving
equipment, including a 45 t Komatsu exca-
vator with a 2,2 m
3
bucket, a Caterpillar
950G sales loader and articulated dump
trucks, to dig out and transport the sand
deposits. It is a condition of Mawsons’
licence that it is not permitted to install
and operate fixed plant on the Whorouly
site. As a result, the company relies very
heavily on mobile plant and equipment at
Whorouly and until recently, was employ-
ing a Terex Finlay 683 Supertrak rinsing
screen and a dewatering screw to wash
and process the sand.
“We were running the sand/slurry out
of the bottom of the 683 into the dewa-
tering screw,” Gilbert says. “A dewatering
screw is good for dewatering but it’s not
good for fines recovery. It did a good job
and it did what it was designed to do but
because the silt and clays in this product
are so low, the more water you put in,
the more fine sand you wash out. There
was nothing we could do to recover it
and we were sacrificing tonnage to basi-
cally recover what sand we could get.
We decided we needed to look for an
alternative.”
Combined wash plant
In 2014, Mineral Washing Systems (MWS),
a subsidiary of Brisbane-based supplier
Finlay Screening and Crushing Systems
began importing Terex Washing Systems’
(TWS) extensive range of sand wash-
ing plant and equipment into Australia,
including the modular AggreSand 165.
The first of these plants was installed in
Dubbo, New South Wales, and at MWS’s
invitation, Gilbert and other Mawsons
personnel visited Dubbo Sands to see the
plant in operation. They were impressed
by the plant and after consultation with
MWS representative James Murphy,
they negotiated a six-week hire with the
option to buy two pieces of TWS plant:
the mobile M1700 rinsing screen and the
modular Finesmaster (FM) 120C compact
cyclone plant.
At the time
Quarry
visited Mawsons
Whorouly, the business had been oper-
ating the M1700 and the FM120C for six
weeks. The combined wash plant had
spent its first four weeks at Mawsons’
Mansfield Quarry operation before being
relocated to Whorouly for the next fort-
night. This enabled Mawsons to test
two different materials on the plant at
separate quarries, as well as trial further
materials brought to Whorouly from
its Seymour and Mildura sites. It also
illustrated to Mawsons the ease of relo-
cating the plant across multiple quarry
sites. According to MWS sales engineer
James Murphy, who worked closely with
Mawsons on the installation of the M1700
and the FM120C, the plant was moved
from Mansfield to Whorouly within three
days, including washdown, demobilisa-
tion, freight, set-up and commissioning.
Murphy says that the M1700 and
FM120C can be operated independently
but when the two machines are run
together, they offer the “exact same wash
plant in principle” as the TWS AggreSand
165, albeit on a mobile platform.
“Some operators will only require
rinsing of, say, crushed aggregates, and
if what is being rinsed away with the
water is not of value to them, they will
discharge any fine material with the
dirty water,” Murphy explains. “But when
a client then wants to recover the sand
being rinsed from the aggregates, as is
the case with Mawsons, we recommend
a modular Finesmaster sand recovery sys-
tem sized appropriately for the tonnage/
throughput required. It’s the combination
of these machines working together that
becomes a wash plant, as opposed to a
rinsing screen working independently.”
According to Mawsons’ Trevor
Gilbert, sand recovery rates for the
operation become more problematic
as the valley gets muddy and clayey.
After a decade of inactivity, Mawsons Concrete
& Quarries reopened the Whorouly sand and
gravel quarry in early 2014.