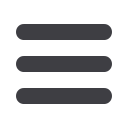
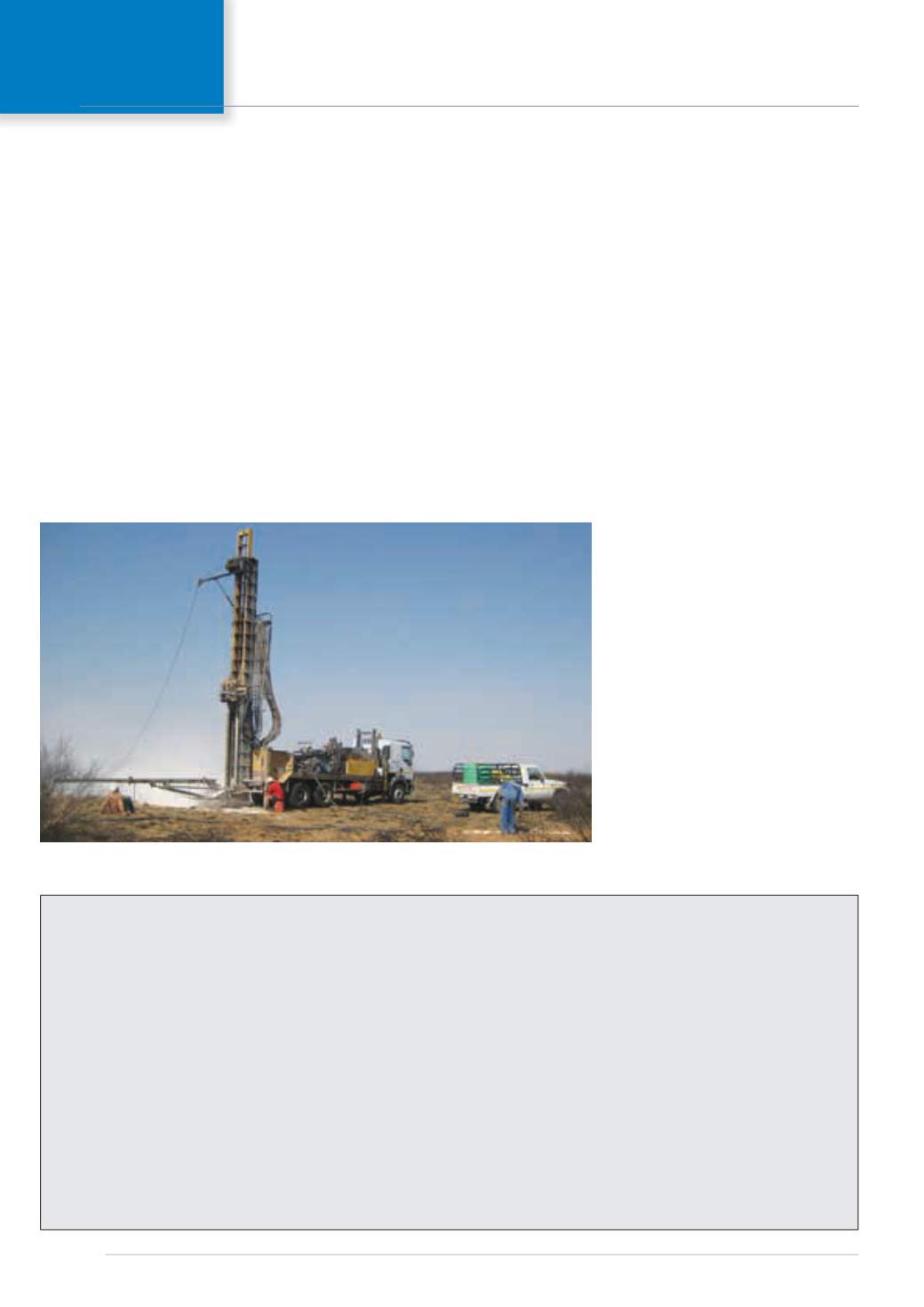
8
MODERN MINING
February 2015
MINING News
ASX-listed Walkabout Resources has
announced the results of a technical
scoping study finalised as part of the
ongoing Pre-Feasibility Study (PFS) on
the Takatokwane thermal coal project in
Botswana. The project has a JORC indi-
cated resource of 7 billion tonnes. The
mine design has focused on the Target
Mining Area which hosts 748 Mt of indi-
cated resource.
The conceptual operation at Taka
tokwane mine contemplates two open-cut
stripmines employing dragline machinery,
each mining some 6 Mt/a of coal. Some of
this product will be upgraded through a
modular two-stage washing plant with
three products delivered for despatch.
Technical scoping study on coal deposit completed
These are an international seaborne coal
product at a calorific value (CV) grade
of 5 500 kcal/kg, a mid-range product at
around 4 800 kcal/kg and a power station
feed of 4 200 kcal/kg.
“It was always important that we under-
stood the optimum profile for mining the
huge Takatokwane deposit,” says Allan
Mulligan, MD of Walkabout Resources.
“We now know that we will be building
large scale, open-cut strip mines employ-
ing draglines and rope excavators that
will produce coal for many years into the
future.
“Similar to those planned for the
Galilee Basin in Australia, these are going
to be long life, stable mines that supply
the emerging economies of the world
with energy for generations to come. The
Takatokwane complex will not be just
a mining site but an entire coal mining
province.”
Non-optimised capex for the project is
estimated at US$767 million with operat-
ing and logistics costs ranging between
US$43 and US$57 per tonne FOB. The
study has been finalised on the basis of
the Trans-Kalahari Rail (TKR) project being
constructed by others as per current plan-
ning and progress.
Although the study has opted for a
12 Mt/a production rate, this can be sig-
nificantly upscaled in modular extensions.
The study also considers the ability of the
project, by virtue of its location adjacent to
the route of the Trans-Kalahari Rail project,
to move coal product both to the west to
Walvis Bay and also southwards to South
Africa.
According to Walkabout, the develop-
ment of the Takatokwane project remains
dependent on the construction of suit-
able rail infrastructure to move the coal
product.
Currently, the Coal Development Unit
of Botswana is managing the Feasibility
Study of the TKR project and this project is
expected to be completed by 2019/2020.
The Takatokwane coal project is a key
input to the viability of the TKR.
Walkabout Resources controls 67 %
of the Takatokwane project through two
joint ventures it has with Botswana-based
companies.
Drilling underway in the Takatokwane project area. The project is located approximately 195 kmwest-northwest
of Gaborone (photo: Walkabout Resources).
Master Drilling awarded landmark Palabora contract
Master Drilling Group Limited has recently
been awarded a shaft construction contract
with Palabora Mining Company Limited
in an industry first for the mining sector.
Master Drilling has designed and built the
RD8 raise boring machine specifically cus-
tomised for the Palabora contract, which
entails the construction of two ventilation
shafts, each 6,1 m diameter and a record-
breaking 1,2 km deep.
“Once completed, the project will qual-
ify as the largest scope of raise boring work
per cubic metre ever embarked on, not only
in South Africa but across the globe,” says
Danie Pretorius, Master Drilling’s CEO.
This unique technology is estimated –
says Master Drilling – to be up to four times
faster than conventional blind sinking
methods, and only requires two persons
per shift working from the safety of an
above-ground control room. Ultimately,
this ground-breaking raise boring machine
is key to pursuing deep-level, large-
diameter shafts in future projects.
Master Drilling’s remote operated shaft
support unit and inspection device will be
used to line parts, or even the full depth, of
the shafts, either during or after the raise
boring process. In comparison to its com-
petitors’ systems, which can only go down
to 350 m with umbilical cords, the Master
Drilling system can line up to a full 1,5 km
deep. The inspection device has the capa-
bility to scan the geometry of the execution
and identify the lithology. This is important
to determine the stability of the shaft dur-
ing or after construction.
Master Drilling recently completed
the 1 km deep Rowland shaft at Lonmin
using similar technology. Accomplished
within budget and schedule and with no
incidents, accidents or damage to prop-
erty, the operation was reportedly a huge
success and the company employed three
local community members as part of its
drilling crew.
“The new crew members will now be
moving with us to the next job as they
have proven their competency and fit to
company culture,” says Pretorius.