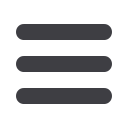

wiredInUSA - March 2016
70
amount of wire lubricant can easily be
controlled in the production process
• Eliminate short feeds before they
occur: RMG’s Autodraw speed control
system matches the consumption rate
of the production machine. All tension
is removed from the feed rolls. Also,
Startgard, Slipgard and Tanglegard
sense any problem with the process and
stop the production machine before a
shortfeed occurs
• Eliminate wire kinks: Wire drawn in-line
is always smooth and straight with a
natural cast and with no kinks
• Employ any coil size or weight: An RMG
wire drawer does all the work of turning
the coil and unwrapping the wire,
thereby eliminating the load on the
feed rolls, regardless of coil size
• Increase overall performance: When
considering
the
improvements
associated with an RMG machine it is
easy to understand why a header line
utilising an RMG in-line wire drawer will
outperform a header line that does not
in both cost and consistency of product
The in-line wire processing equipment is
used by many manufacturing processes
including fastener production, nail making,
wire bending, concrete products, steel bar
processing, welded wire products, screw
machine parts and wire straightening and
cutting. On display will be the Model 500
in-line wire drawer.
Rockford Manufacturing Group – USA
Website:
www.rmgfelm.comSpirka Schnellflechter and Wardwell
Braiding
Booth: 09B33
The Type DF braiding machines are used
for screening of coaxial cables and other
conductors and cables with copper or
galvanized steel wires in a diameter range
of 0.05 to 0.3mm. The DF 16 A on display will
be configured for braiding of fine wires in
range of 4x.05mm.
This will also be demonstrated with a new
control system, which provides the following
features and advantages to customers:
• New generation of PLC, HMI and drives
• Optimized and user-friendly operating
system
• Expanded pitch range
• Optional energy and temperature
measuring system
• Optional remote control and diagnostic
system
• Upgraded empty bobbin detection
system
The machine will be presented with
options for pay-off and take-up to
demonstrate the flexibility of the system
for different application ranges and cable
specifications.
This braiding line offers a wide range
of applications and increased flexibility
in screening processes. The integrated
concentric taper features optimized
regulation for precise pre-setting of tape