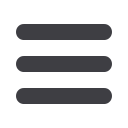

15
Chemical Technology • April 2015
Reaching the cooled pump housing, the vaporised
pump fluid condenses on the cold wall. The liquid fluid runs
downward and returns into the boiler from where it will be
evaporated again. Why does this principle pump at all?
Figure 2 shows a detailed view into the pumping mecha-
nism of the diffusion pump. We can see the vapour jet on
its way from the jet system toward the water-cooled wall.
The jet consists of ‘degassed’ fluid vapour, which means
it only contains extremely low partial pressure of the gases
that should be pumped. The area above the vapour jet,
therefore, contains a much higher partial pressure of the
gas. Driven by partial-pressure difference, the gas from
above diffuses into the jet stream to compensate.
The jet stream will push the gases toward the cooled
wall and the next nozzle stage of the pump. Finally reaching
the exhaust side of the pump, the gases will be pumped
away by the backing pump. The vacuum inside the boiler
will ensure that the reboiling fluid will contain the lowest
partial-pressure of gases again.
Energy-saving measures
The following measures have been identified as having the
highest influence on the power consumption of a diffusion
pump:
1. Pump design features
2. Electronic regulation of heater power
3. Regulation of cooling water
4. Housing insulation
5. Correct heater adjustment according to the selected
driving fluid
6. Standby operation/intelligent process management
Pump design features
It is obvious that the total diffusion pump must already be
designed to minimise consumption. To save energy and
consumables, modern diffusion pumps are optimised with
some design features:
• Heaters are positioned inside the boiler
• Reduction of heat-transfer losses, thereby lowering
power demand
• Grooved pump body with built-in cooling-water coils
• Reduction of weight and therefore total energy for
initial heating
• Optimisation of contact surface/heat-transfer efficiency,
thereby reducing cooling-water demand
• Water-cooled cold-cap baffle at inlet
• Reduction of fluid backstreaming into the vacuum
chamber, thereby reducing fluid losses
• Water-cooled fore-vacuum baffle at outlet
• Reduction of fluid losses into the fore-vacuum line
Electronic regulation of heater power
One general statement to first consider: More heating power
does not automatically result in more suction speed!
As previously described, the main driving force for the
pumping mechanism is the partial-pressure difference
PUMPS & VALVES
Loading a vacuum furnace.
Image: Bodycote
www.bodycote.com