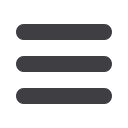

EuroWire – March 2009
92
technical article
PVC improvement: a new
range of eco-compounds
By Claudia Attanasio and Laura Colloca, B&B Compounds, Italy
Abstract:
This paper covers a new range of
compounds using nanofiller that exhibit
lower environment impact both in their
production and throughout their life
cycle. The compounds show resistance
to flame, reduction in smoke density and
HCl emission, optimal electrical properties
(as high-volume resistivity values), and a
high thermal stability with a significant
reduction in density and therefore weight.
The products are free from dangerous
substances such as phosphoric plasticisers,
DEHP or heavy metals.
1 Introduction
With such a large variety of end uses,
cables have to fulfil very special
requirements. Many different polymers
have been developed during the last few
decades to meet the needs of various
applications. These polymers can be
classified roughly into thermoplastics,
thermoplastic
elastomers,
elastomers,
cross-linked thermoplastics and cross-linked
elastomers. The choice of the appropriate
polymer depends on the physical and
chemical compound properties defined in
the cable standard.
The excellent electrical and mechanical
properties of PVC make it an ideal material
for sheathing, insulation and protection
of cables. PVC-covered cables have a
service life of decades, much longer than
can be guaranteed by any other type
of material. The mechanical resistance
and the robustness of the material are
important for any installation, whether
underground, within buildings or under
pavements. The electrical characteristics
of PVC make it the ideal material for cables
for low and medium voltage up to 5kV. The
normal operating temperature range is up
70°C, but can be increased to 105°C using
specialised formulations. The PVC remains
stable down to –40°C and is impermeable
to humidity.
The cables used in industrial plants, power
stations, multi-store buildings, hotels,
subway tunnels, road tunnels or in vehicle
construction must comply not only with
the electrical and mechanical standards
corresponding to the characteristic of the
material, but also to exacting standards
of flame retardancy. In case of fire, the
materials used must also demonstrate
a reduction in density, toxicity and
corrosiveness of combustion smokes.
Many studies have shown that the
initiation and development of accidental
fires are complex matters. A number of
factors must be taken into account in
assessing the contribution of any one
material to a fire situation.
The several plastics materials used in the
building and construction industries have
differing reactions to fire. The high chlorine
content of PVC polymer reduces its
ignitability and also the heat it contributes
to a fire, in comparison with other plastics.
As the basic polymer is diluted with
additives, the fire performance changes.
High concentrations of organic materials
will increase flammability; high con-
centrations of inorganic materials will
reduce it. PVC formulations, like other
natural and synthetic materials, give rise to
smoke and to toxic gases when they burn.
Significant reductions in the emission of
smoke and hydrogen chloride may be
achieved by the use of special additives.
Independent studies have concluded that
PVC fire gases are not significantly more
toxic than those from other common
building materials.
It has been recognised in a number of
studies that the substitution of traditional
building materials by PVC brings no
significant change to the hazards of
accidental fires in buildings.
In a detailed assessment of the overall
fire-performance of a material many
factors must be taken into account:
Ignition
: PVC is resistant to ignition. The
temperature required to ignite rigid PVC is
more than 150°C higher than that required
to ignite wood. The ignition resistance of
common flexible PVC formulations is lower,
but with specialised formulations it may be
significantly increased.
Flammability
:
Once a material has been
ignited, the associated hazard will be
related directly to its flammability. One of
the most reliable quantitative small-scale
flammability tests is the Limiting Oxygen
Index test, which measures the limiting
concentration of oxygen in an oxygen/
nitrogen mixture necessary for sustained
combustion. A material with a LOI value
above 21 (air contains 21% oxygen) should
not burn in air at room temperature, and a
value above 25-27 means that the material
will only burn under conditions where very
high heat is applied to it.
Rigid PVC has an oxygen index of 45-50,
compared to 21-22 for wood and 17-18
for most thermoplastics. Oxygen index
values above 27 can easily be attained
with flexible PVC. The significance of this
is that most rigid and flexible PVC will not
burn alone without the application of heat
from another source.
Smoke density
:
Decreased visibility is a
serious concern in a fire, because both
escape from the fire and rescue by fire
fighters is more difficult. The main way in
which a fire decreases visibility is by the
release of smoke. However, decreased
visibility is the result of a combination of
two factors: how much material is burned
in the fire (which will be less if the material
has better fire performance) and how
much smoke is released per unit of material
burned. Several empirical parameters
have been proposed to compensate for
incomplete sample consumption under
testing conditions. One of them – known
as the smoke factor – recently has been
used with small-scale rate of heat release
calorimeters. It combines the two aspects
mentioned above: light obscuration and
rate of heat release.
Euro ire – March 20 9