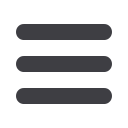

118
Limitations
The inventory system has physical, economical and administrative limitations.
The physical limitations are for example storage room, material handling capacity and
personnel. The economical limitations are, for instance, the limited operating capital.
The management of the company can set some limitations to the inventory systems
such as setting the service level target near one hundred percent for certain articles.
Costs
The decision problem of material management concerning the inventories is to
define the optimal inventory level by the benefits and costs of the inventories. The costs
of an inventory system can be divided into four groups:
Purchasing costs
These include the price and possible delivery costs. In the product inventory, it
equals the own cost price of the production (= direct labour and material + the general
costs of the production).
Order/setting costs
These include all costs caused by issuing one order. Order/setting costs are not
dependent on the batch size. The order costs come from preparing the order and the setting
costs from setting the production to produce the ordered batch into the product inventory.
The holding costs of the inventory
These can be determined as costs which alter when inventory levels alter. The
holding costs include the following components:
• Decreasing of the inventory value for example because of the physical
deterioration, vanishing or technical-economical ageing.
• Physical costs of the storage which include the handling costs, the operational
costs of the inventory (heating, cooling etc.) And the protection costs of the
material.
• Insurance costs are in the long run dependent on the inventory value.
• Capital costs are in principle the alternative costs of the capital bound into
inventories; in practise it is the interest of the short-term external capital or
marked deposition.
It must be noticed that the holding costs of the inventory depends on excluding
the capital costs on more or less the physical nature of the stored material. The holding
costs then vary significantly between different lines of business. Most of the estimations
vary between 20-40% of the inventory investment per year.
Stock-out costs
These are caused by the situations when the inventory is unable to serve the
production (internal stock-out) or the customer (external stock-out). These costs include
the after-delivery costs caused by delivery delays, sales lost because of the stock-out and
the loss of good will (= bad will) because of the stock-out. Usually it is very difficult to
determine the stock-out costs. The company management have to set a service level to
the inventories and this level must be met.