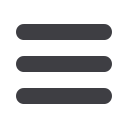

Feature
Wire cleaning & treatment
May 2016
52
www.read-eurowire.comA unique partner for
wire cleaning
Candor Sweden AB specialises in
advanced wire cleaning and plating
plants
for
various
applications.
Founded as a chemical supplier, its
combination of know-how in chemical
processes and advanced equipment
for cleaning and plating of wire makes
it a good choice in the market.
It has a wide selection of wire
cleaning plants to offer, such as hot
water spray cleaning, ultrasonic
cleaning and electrolytic cleaning.
Which technology to use is a balance
between wire speed, cleaning
requirements, type of lubricant used
and environmental aspects.
In many cases, especially for high-
speed applications, the processes
can be combined as separate steps
after each other in a plant. By this
way a hot water cleaning unit can be
dedicated to remove sodium-based
lubricants and an acid ultrasonic
or electrolytic process can make
the fine tuning of the already
pre-cleaned wire if required.
Candor Sweden AB – Sweden
Website
:
www.candorsweden.comOver the past few years, Boockmann‘s still relatively new
Helicord® technology for wire and cable surface processing has
been implemented successfully in industrial production lines.
Particularly noteworthy applications are welding wire finishing,
removal of misprints from cable, removal of metal particles from
strands, removal of drawing lubricants and metal particles before
extrusion, and various cleaning and lubricating applications in
special wire such as for food or medical use.
The main advantages of Helicord as compared to other
technologies are the multiple 360° contact between wire and
cleaning medium, a constantly refreshed cleaning medium, and
efficiency of the process being independent from wire speed.
Helicord machines can be equipped with a pump and heating,
and are available as one-step (NB57) or two-step (NB58) models,
allowing for up to two subsequent processes (eg abrasive
cleaning and subsequent finish application). Special models for
low tensile forces, ie small wire diameters, are also available.
NB57W and NB58W models
were designed for installation
directly before the winder. A
traversing process zone that can
be connected to the traverse of
the winder allows for minimum
space requirements and avoids
stress on the wire after the
finishing process.
The most promising application
is welding wire finishing with
simultaneous coating and re-
moval of particles. New types of fully impregnated finishing
cords used to transfer active components (such as lubricants,
corrosion inhibitors and arc stabilisers) have been a huge
success.
Boockmann Engineering GmbH – Germany
Website
:
www.boockmann.comThe request for cleaning processes in the
wire industry is continuously increasing,
along with the need for increased quality
requirements.
Cleaning is used for stainless steel, low
and high carbon steel, aluminium alloy,
and copper wire to remove calcium and
sodium stearate lubricant coming from
the dry drawing machine, lubricant oil
from a wet drawing machine or forming
process, etc.
Ultrasonic cleaning has become popular
and has been adopted by many wire
producers worldwide.
Ultrasonic cleaning uses high frequency
sound waves. During the activity, called
cavitation, micro-size bubbles form,
grow and implode due to alternating
positive and negative pressure waves.
Just prior to the bubble implosion, there
is a tremendous amount of energy stored
inside the bubble itself.
The implosion event occurring near a
hard surface changes the bubble into a jet
which travels at a speed of approximately
400km/h towards the hard surface.
Because of the inherent small size of the
jet, ultrasonic cleaning has the ability
to reach into small crevices and remove
entrapped soils very effectively.
The basic components of an ultrasonic
cleaning system include some ultrasonic
transducers, an electrical generator and a
tank containing the cleaning solution.
The ultrasonic generator converts a
standard electrical frequency of 50 or
60Hz into the high frequencies required.
The higher the frequency, the smaller the
bubbles during the cavitation will be.
The transducers are constituted of PZT
elements (Pb-Zr-Ti) which converts the
electrical energy in mechanical vibrations
by piezoelectric action.
Generally speaking, for the majority of
the applications in the wire industry,
alkaline solutions are preferred to remove
oily matter, and phosphoric acid-based
solutions preferred to remove stearate
soaps.
Higher temperatures result in higher
cavitation intensity and better cleaning.
However, if the solution temperature
closely approaches the boiling point of
the solution, the liquid will boil in the
negative pressure areas of the sound
waves, reducing or eliminating the
cavitation effect. Working around 60°C
(140°F) offers an excellent compromise.
Sirio recommends that the baths be made
of polypropylene, with one reservoir and
one overflow bath in order to avoid any
inflexion of the wire.
One vertical pump transfers the solution
from the reservoir to the overflow bath.
SirioWire Srl – Italy
Website
:
www.siriowire.itHigh frequency solution
▲
▲
View of air wiping and the rinsing device
▼
▼
Helicord® technology has been
successfully
implemented
in
industrial production lines
Extraordinary results
▲
▲
A Candor MIG wire cleaning plant with the
Candojet HW as pre-cleaning followed by
an ultrasonic acid treatment for an effective
cleaning at high speed up to 15-20m/s