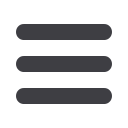

July - August 2015
MODERN QUARRYING
11
ON THE
COVER
The DCT 200 dust collector provides strong dust suction capacity and excellent
dust suppression. There are 20 filter elements with a total filter area of 20 m
2
.
hammer market around
tests we carried out at operations around the coun-
try.” (
See Table 1, 2 and 3
).
The drill rig was supplied to drill and blast spe-
cialist Eire Contractors based in Durban, KwaZulu-
Natal. It was also tested in quarrying and opencast
mining applications in Pietermaritzburg and Piet
Retief in Mpumalanga in September and October
last year.”
“Eire was extremely happy with the savings on
diesel, and reported that the rig easily drilled holes
between 140 mm and 152 mm in diameter with
the rig’s power, speed and fuel efficiency meeting
the company’s objectives.” At the coal operation
in Piet Retief, Birnie says the drill achieved about
200 m/hour during the practical applications.
John Moffat, founder and Eire Contractors CEO
confirms that the rig’s power, speed and fuel effi-
ciency more than meets the company’s objectives
of achieving maximum productivity with minimum
input. “In addition to substantial savings on diesel,
the rig drilled the holes with ease.”
Company MD Matthew Moffat agrees:
“Choosing the right equipment can be a tough
decision, but the resultant low maintenance and
extended life delivered by Atlas Copco equipment
for optimum uptime and production levels, makes
the decision an easy one.”
In the hard rock test applications at the
Pietermaritzburg quarries, which included granite
and quartzite, the PowerROC T50 achieved a drill-
ing capacity of between 42 m/hour and 44 m/hour.
“Eire Contractors has not only purchased the
demo model, but an additional five more units
with Anglo American placing an order for three
machines for its Kumba iron-ore facility at Sishen
in the Northern Cape. We are also in negotiations
with the mining and quarrying industry for other
orders. Our aim is to supply 15 machines within the
next 12 months and 25 units to the local industry
by 2017,” Birnie says.
The straight-forward modular design includes
simplified hydraulic and electrical systems for
easier operation and maintenance. “What makes
the drill rig particularly attractive, especially in
this tough economic climate, is its extremely fuel-
efficient capability,” he confirms. “The machine’s
effective management system allows for low fuel
burn at full production, giving fuel burn as low as
27 ℓ/hour on large holes; something that is
unmatched by similar-sized machines in the
industry.”
The machine’s Tier 3 diesel power pack delivers
261 kW at 1 800 rpm, providing more tons per litre
of fuel with a direct positive result on productivity.
“We have found a seamless balance between effi-
cient operation and high performance while also
caring for the environment by conforming to emis-
sion standards,” he adds.
Discussing the drill rig’s high penetration capa-
bility, Birnie says this comes from the powerful COP
3060 30 kW hydraulic rock drill – a proven high
performance unit in the Atlas Copco range. “While
output is dependent on mineral type and location,
the drill rig/rock drill combination’s output capa-
bilities are impressive ranging from 200 m/hour in
medium rock (coal) to 70 m/hour in hard rock. Even
in the most extreme environments and the hardest
of material, the machine is capable of a remarkable
40 m/hour.”
In terms of hole diameter, the machine is capa-
ble of remarkable power and output, drilling holes
ranging from102-152mm in size and 35m in depth.
Diagram shows the five hydraulic pumps.
No 1 and 2 are piston pumps. No 3, 4 and
5 are gear pumps.