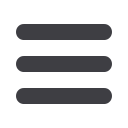

S
eptember
2011
155
›
A
rticle
Forming tubes and strategies to
minimise waste
By Phillip Aspinall, general manager, AddisonMckee
GLOBAL leader in the design, manufacture and supply of the world’s
finest tube bending and endforming technologies, AddisonMckee of
Lancashire, UK is also gaining a global reputation for forming unique
strategies to deal with the bane of the tube former’s life: ‘off-fall’ or,
more prosaically, unusable material or waste.
In a world in which budgets grow ever tighter while global steel
prices continue to soar, the issue of waste is increasingly being seen
as one of the industry’s most pressing problems and, alongside
accelerating manufacturing times, negating waste has become
one of AddisonMckee’s principal preoccupations in the design and
manufacture of its world-leading tube bending solutions.
So, while the most obvious bugbear for anyone involved in the tube
bending process will be perishables, such as wiper dies, mandrels
and lubricants, a peek into the scrap bin sitting beside the tube trim
machine in any tube forming facility will quickly establish where the
biggest problem lies, namely in bending ‘off-fall’.
Of course it is impossible to eliminate ‘off fall’ altogether. However,
there are ways and means to minimise the amount of ‘off fall’
incurred in bending and make significant cost savings in the
process. And AddisonMckee is at the very forefront of developing
cost-saving strategies to minimise material waste.
Making theoretical tube calculations
There are three main components that must be considered when
calculating the length of material needed to produce a bent part (see
Figure 1). These components are:
•
Clamping stock
– the extra material needed to sufficiently grip
and bend the first bend of the component.
•
Component(s) length
- the developed length along the centreline
of the component, including material needed for subsequent
end-forming operations and, if there are multiple components
being bent in one tube, material required for parting.
•
Collet stock
– the extra material needed to sufficiently grip the
tube in order to rotate and position for bending.
Examining sample figures, based upon tube centreline data of XYZ,
YBC
60.3 diameter x 1.75mm wall, 409SS
X
Y
Z CLR Y
B C
150.70 67.60 -7.45
130.40 44.50 0.00 63.50
23.97
13.78
94.10 0.00 0.00 63.50
19.61
-98.62
50.79
15.50 0.00 0.00
48.45
0.00
Determining clamping stock
When determining clamping stock, several factors must first be
considered:
•
Will the bender have boost capabilities?
•
Does the product require a square end?
•
Cosmetic details (grip type – saw tooth, carbide spray)
•
Will the extra clamping stock be removed with a saw or stab-cut
type operation?
Where a bender is equipped with boost and it is intended to use the
minimum grip length of 1D, the end of the tube will be out of square.
A good rule of thumb, therefore, is the first straight must be at least
1.5D before the end of the tube is not pulled out of square by the
bending process. If boost is not used, the first straight should be at
least 2D.
Looking at the sample data, we see that the first straight is 23.97mm.
This is a 0.40D straight (23.97/60.3). Assuming the bender used
does not have boost capabilities, we will need to add enough extra
stock to increase the first straight to 2D.
Clamping stock formula:
•
OD = Tube outside diameter
•
SLx = Straight length (where x is the first straight)
Figure 1