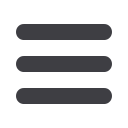

S
eptember
2011
157
›
A
rticle
Figure 3
Determining collet depth
When determining collet depth stock, several factors must be
considered:
•
Rotational torque from tube
•
0.5D minimum
•
Bender manufacturer’s standards
Again, the idea is to reduce the amount of tube needed to
sufficiently hold the tube during the bending process. For the sample
calculations, we will use the 0.5D minimum.
Collet Depth Formula:
TUBE OD * 0.5
Using the sample data:
Collet Depth = 60.3 * 0.5 = 30.15
Collet Depth = 30.15mm
Collet stock length
Once all the tooling lengths are determined, it is possible to
calculate the additional material need for the collet end. At this point
it is necessary to decide whether or not boost will be used.
With Boost
(collet will hold tube during the entire bending cycle):
•
PL t = Pressure die length (where t is the total length)
•
PLr = Pressure die length (where r is the remaining length from
tangent after the last bend is made) (see Figure 4)
•
WL = Wiper die length
•
CD = Collet depth
•
SLx = Straight length (where x is the last straight)
•
CF = Clearance factor (5mm)
•
ALy = Length along the arc (where y is the last bend)
•
LL = Limiter length (Distance from tangent at which the collet
housing will encounter interference)
Arc length formula:
AL y = (Π * CLR / 180 * DEGREE OF LAST BEND)
Pressure die length remaining formula:
PL r = PL t - AL y
Limiter Length Formula:
LL = WL or PL r (whichever is greater)
Collet stock length formula:
LL + CF + CD - SL x
Using the sample data:
•
WL =100mm
•
PLt = 176mm
•
SLx = 48.45mm
•
CD = 30.15mm
•
ALy = (Π * CLR / 180 * 50.79) = 56.29
•
PLr = 176 - 56.29 = 119.71
•
LL = 119.71 (PL r is greater than WL)
Collet Stock = LL + CF + CD – SL x
Collet Stock = 119.71 + 5 + 30.15 – 48.45
Collet Stock with Boost = 106.41mm
Note: If the calculated collet stock is a negative number then no
additional collet stock material is required.
Money-saving strategy 4
For part configurations, where the deepest bend is not the last
bend, the pressure die is typically extended past the wiper as the
bend cycle completes (see Figure 4). When this situation occurs, a
‘split pressure die’ should be considered. The two halves will act as
one die until the last bend. Before the last bend is positioned, the
rear pressure is lifted out of the way, allowing the collet housing to
approach further towards tangent (see Figure 5).
Figure 4
Figure 5
Without boost
(collet will release the tube during the last bend):
When bending without boost, the pressure die length is not a
consideration. As seen in Figure 6, the pressure die can be ‘backed’
out of the way while the tube is positioned for the last bend. As
the tube is positioned, the wiper die becomes the only point of
interference. Once the tube is in position and clamped, the collet is
retracted and the pressure die is advanced.