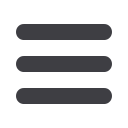

66
S
eptember
2011
www.read-tpt.com›
T
echnology
U
pdate
GEORGSMARIENHÜTTE GmbH (GMH)
is a European producer of special bar
quality (SBQ) for the automotive industry.
The company will optimise the production
process of its bar mill in Georgsmarienhütte,
Germany, to permanently improve the
quality of its products according to market
requirements.
GMH placed an order with the family-
owned company Friedrich Kocks GmbH &
Co KG (Kocks), located in Hilden, Germany,
to extensively modernise and extend a three-
roll reducing and sizing block (RSB) that was
commissioned in 2002.
The order comprises the delivery and
commissioning of a real-time closed-loop
control system (SCS – size control system)
specifically developed for the RSB, which
reaches the optimum operating state of the
block as quickly as possible, and keeps the
production quality of the rolled product on a
constantly high, reproducible level.
As another part of the project, the existing
five-stand three-roll reducing and sizing
block will be extended from five to six stand
positions, and all stand positions will be
modified to incorporate the newly developed
three-roll stands, adjustable under load
(AUL). The SCS controls the roll gap of these
stands continuously to optimise the already
very tight finished size tolerances.
The upgrade to the new generation of
the three-roll reducing and sizing block
results from the many successful rolling
tests under real rolling conditions, which
have been carried out by Kocks in close
co-operation and intensive support by GMH
at the location in Georgsmarienhütte. Prior
to these rolling trials Kocks had carried
out extensive research and development
in the mechanical field as well as in the
automation sector.
Whendevelopingbothcomponents,Kocks
focused particularly on the fact that reducing
and sizing blocks already in operation could
be equipped with the SCS as well as with the
new stand type AUL. The new stand AUL is
based on the successful ‘heavy duty’ stand
with a nominal roll diameter of 370mm and
has identical external dimensions as well as
drive couplings.
The combination of SCS and stand AUL
will be the basis for the latest generation of
the RSB. This design will both simplify the
operation of the RSB and also ensure tight
tolerances over the whole length of each
individual bar for the complete production
range. Georgsmarienhütte is the first mill to
implement this change, and commissioning
is planned for summer 2012.
Friedrich Kocks GmbH & Co KG
–
Germany
Fax: +49 2103 54028
Email:
v.d.heiden@kocks.deWebsite:
www.kocks.deNew generation of reducing/sizing block
A step ahead
technology
AFTER 14 years of intense technical
development, marketing and sales strategy
Axxair is recognised as a key player in
the orbital market, covering more than 35
countries through its network of distributors
and subsidiaries. Axxair offers the ‘global
process’, which is themost complete solution
on the market for the orbital preparation
and welding of tubes in workshops and
on site. Its global offer is largely covering
the semiconductor, the pharmaceutical, the
food and beverage industries as well as
acting in chemical and petrochemical, solar
and desalinisation of water.
The innovating character residing in the
principle of interchangeability of the various
tools: one machine for three applications,
global process Axxair; biggest range of
diameter in cutting machines (from 5mm to
1,100mm); new and patented process for
beveling with carbide tips; orbital welding
in prefabrication, unique in the market,
completed by closed and open heads as well
as tube-to-tube sheet heads; new design for
cutting, bevelling and welding machines.
Axxair
– France
Fax: +33 4755 75080
Website:
www.axxair.com