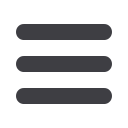

62
S
eptember
2011
www.read-tpt.com›
T
echnology
U
pdate
OLYMPUS has introduced its latest
ultrasonic industrial NDT system: the
In-Line ERW Tube Inspection System
uses advanced phased array technology to
inspect weld seams and the heat-affected
zone (HAZ) of electrical resistance welded
(ERW) tubes.
The main advantage of the system is
that it performs ERW tube inspections using
advanced phased array technology in place
of conventional ultrasound technology.
Phased array (PA) offers broad sector
coverage of the HAZ while maintaining
constant amplitude. This solution provides
constant amplitude detection within the
entire inspection area, even when there is
significant weld seam movement relative
to the probes. In addition, PA technology
permits electronic optimisation of the beam
shape in order to enhance the detection of
small defects such as penetrators.
The ERW Tube Inspection System is
capable of inspecting pipes with diameters
ranging from 60 to 245mm (2.375" to
9.625") and wall thicknesses from 2 to
16mm (0.079" to 0.63"). The system has
a maximum inspection speed of 1.5m/s
(295ft/min).
The Olympus mechanical solution
for ERW tube inspection is based on a
small automated bridge (gantry type)
that positions the inspection head in-line
or off-line when performing inspections,
automatic calibrations, calibration checks
and maintenance operations.
While the system’s main function is to
detect longitudinal flaws using a cylindrical
phased array probe located on each side
of the weld, a third cylindrical phased array
probe located on top of the weld and firing
at 0 degrees may be used for weld profiling
to create a true side view of the weld for
simple and fast profile analysis.
This third PA probe and a unique
patented algorithm based on time-of-flight
analysis enables the system to perform
automatic detection of the scarfing
area and send feedback to the PLC for
automatic adjustment of the position of
each inspection head. Olympus NDT
manufactures non-destructive testing
instruments that are used in industrial
and research applications ranging
from aerospace, power generation,
petrochemical, civil infrastructure and
automotive to consumer products.
Leading-edge testing technologies include
ultrasound, ultrasound phased array, eddy
current, eddy current array and X-ray
fluorescence.
The company’s products include flaw
detectors, thickness gauges, in-line systems,
automated systems, industrial scanners,
pulser-receivers, probes, transducers and
various accessories. Olympus NDT is also
a distributor of remote visual inspection
instruments and high-speed video cameras
in the Americas. The company is based in
Waltham, Massachusetts, USA, and has
sales and service centres in all principal
industrial locations worldwide.
Olympus NDT
– USA
Fax: +1 781 419 3980
Website:
www.olympus-ims.comERW tube inspection system
Unispeed range
ACCURATE pre-assembly of the fitting cutting ring and the
37° flaring of the steel tube is paramount to the safety of any
system using DIN 2353 and SAE J 514 fittings joints. Incorrect
assembly of the cutting ring and inaccurate flaring of the tube
might jeopardise the system and, in extreme cases, cause injury
to property and persons. To avoid this, Italian company OP
proposes various Unispeed series models.
The new Unispeed USFL
24/37 allows preassembling
DIN 2353 rings and 37°
flaring of hydraulic tubes up
to 42mm diameter and a
maximum thickness of 4mm.
The machine is equipped
with a double working level:
an upper level for bends up
to 180° and a lower one for
standard tubes.
The electronic control
ensures
enhanced
performance and makes
the Unispeed USFL 24/37
ES particularly suitable for
volume production.
OP Srl
– Italy
Email:
sales@op-srl.itWebsite:
www.op-srl.itThe new Unispeed USFL 24/37 ES