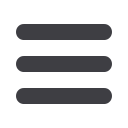

S
eptember
2011
59
›
T
echnology
U
pdate
SICA’s Everbell 160 range of belling
machines has been extended recently
with the addition of the Everbell 160 DE
version, designed specifically to process
pipes of different length simultaneously.
The machine is suitable in double-extrusion
lines producing PVC-U pipes used as
cable conduit and for small diameter indoor
sewage systems.
Everbell 160 DE belling machines
process pipes with a minimum diameter
of 32mm up to a maximum of 160mm, in
lengths between 150mm and 3m (plus
socket). If requested, the machine can be
supplied in versions that accommodate
pipes up to 6m in length. The machine’s
belling system is the same as that of the
other Everbell 160 models, with contact
ovens and an air-blowing forming station.
Sockets can be solvent-cement or O-ring.
Double-extrusion of small diameter pipes is
associated typically with PVC-U production
lines; but when fitted with the appropriate
belling tool heads, the Everbell 160 DE can
also process PP and HDPE pipes.
The DE system uses a dual conveyor with
power driven rollers and is equipped with a
pick-up device, aligned with but operating
entirely independently of the pipe infeed
and management system. It distances the
cut pipes, stops them, and position them in
correspondence to the belling machine head.
A mechanical device picks up the positioned
pipes, and thanks to special buffer stations,
is synchronised automatically with the cycle
times of the machine. Pipes can be received
and organised even when the extrusion
speeds of the two lines are different, or when
the length sequences of the cut pipes are
different.
The electronic master control unit of the
machine utilises advanced software logic to
control the distribution of the pipes entering
from the two lines, according to the different
lengths of the cut pipes, to optimise the
quantity of pipes produced and socketed.
Like the Everbell 160 models, besides
being designed for the installation of multiple
machines in the same double-extrusion
line, the Everbell 160 DE belling machines
can be integrated with automatic ring-fitting
units (masterfit type), and with downstream
packing machines (multipack type), which
bundle and palletise the finished pipes.
Operating with or without other
machine units, the Everbell 160 DE model
will guarantee maximum flexibility and
automation when handling and processing
pipes produced in various lengths and
extruded at different speeds.
Sica
– Italy
Website:
www.sica-italy.comDouble-extrusion of different length
pipes with the Everbell 160 DE
Laser seam
tracking for
automated
welding
THE bottom line for companies
manufacturing welded products is to
achieve the highest quality at the lowest
cost. A measure of how well this is being
achieved is the metric called overall
equipment effectiveness (OEE). Servo-
Robot has released the new Auto-Trac/
PWP laser vision seam tracking system
that improves weld productivity, quality
and uptime, which are the three factors
influencing the OEE metric.
The company states that Auto-Trac/
PWP can achieve new levels of welding
performance while being simple to operate,
comparing its ease of use to that of Apple’s
user-friendly iPad. The system can be
installed on new equipment, or can be
easily retrofitted to existing welders that
are manually operated or use a mechanical
probe for guidance. The heart of the system
is the high-speed digital laser camera head,
which is claimed to be the most powerful
for its size on the market. It has a large
field of view combined with high resolution
that allows the system to handle products
ranging from thin sheet metal to 50mm
thick steel. In the past, a camera had to
be optimised for either small or large weld
joints, but could not do both; this is no
longer a limitation.
Auto-Trac/PWP has a range of new
features that directly improve performance
when welding products ranging from storage
tanks and ships to bridges. In addition to its
main task of seam tracking, the system’s
ability to monitor the overall welding process
provides useful data to facilitate Six Sigma
continuous improvement efforts. Information
includes part fit-up variability, system uptime
and productivity metrics.
Servo-Robot Inc
– Canada
Fax: +1 450 653 7869
Email:
sales@servorobot.comWebsite:
www.servorobot.comServo-Robot’s
Auto-Trac/PWP
laser vision seam
tracking system