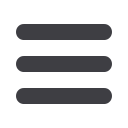

56
S
eptember
2011
www.read-tpt.com›
I
ndustry
N
ews
LE.DI.CA. Srl ,
Have produced since 1981 welding equipment
for longitudinal tube and pipe. We have good
solutions for increasing your productivity and
quality. We can increase the speed of the
Tricathode TIG-TIG-TIG up to 50% , and can
weld in one pass head to head 12,70 mm with
our Plasma torch, all with our new pulsed
power source 6000 hz 400amp 100%.
COMBO WELDING EQUIPMENT
PLASMA-PLASMA-TIG + TIG-TIG-TIG - ARC
OSCILLATOR - WIRE FEEDER
MOTORIZED LASER SENSOR TRACKER
www.ledica.itViale Toscana 46/10 - 20089 Rozzano (MI)
Tel :0039-02-89202078 - Fax :0039-02-89200197
E-mail:
info@ledica.itLE.DI.CA. srl
AUTOMATIC WELDING SYSTEMS
JM EAGLE, a manufacturer of plastic pipe,
has been honoured by the US Environmental
Protection Agency for achieving ambitious
energy efficiency goals at four of its facilities.
The news comes as the EPA released
the results of the ‘Energy Star Challenge
for Industry’, an initiative it began last year
to encourage US manufacturers to improve
energy efficiency. JM Eagle submitted three
facilities to the challenge, but was credited
for meeting reduction goals at four of its
facilities.
“At JM Eagle, we are deeply committed to
a cleaner, greener environment,” commented
Neal Gordon, vice president for marketing.
“Today’s news underscores how devoted
we are to improving energy efficiency
and reducing greenhouse gas emissions.
We are delighted that four of our facilities
are among the very few manufacturing sites
in the nation that were able to meet the
extremely rigorous Energy Star Challenge.”
According to the EPA, the Energy Star
Challenge is “a national call-to-action to
improve the energy efficiency of America’s
commercial and industrial buildings by 10 per
cent or more.”
The EPA’s goal is for manufacturers to
make these energy efficiency improvements
over the next five years.
“The principles we have learned through
the Energy Star Challenge over the last year
are extraordinary,” said Mr Gordon. “We are
working to incorporate those practices in all
of our facilities across the nation.”
Around 240 manufacturing sites have
signed up for the challenge so far, but just
34 facilities – including JM Eagle’s four – met
the emission reduction goals, according to
the EPA. JM Eagle’s facilities achieving the
recognition are based in Hastings, Nebraska;
Wharton, Texas; Butner, North Carolina; and
Stockton, California.
With 22 manufacturing plants throughout
North America, JM Eagle manufactures a
wide array of high-grade, high-performance
polyvinyl chloride and high-density
polyethylene pipe across a variety of
industries and applications, including utility,
solvent weld, electrical conduit, natural gas,
irrigation, potable water and sewage.
JM Eagle
– USA
Website:
www.jmeagle.comPipe maker recognised for efficiency
Barrett Steel expands into Houston, Texas
BARRETT Steel is expanding its global
reach by establishing a presence in Houston,
Texas, to serve the oil and gas industry in the
Gulf of Mexico and Brazil. From its purpose-
built 33,000ft
2
facility, Barrett Steel Energy
Products will specialise in raw materials
for the downhole tool and equipment used
in the oil and gas industry, including solid
bar, hollows and tubing that meet the
requirements of all oil patch grades.
The move is a demonstration of the Barrett
Steel Group’s commitment to new markets
and to cementing stronger relationships with
overseas customers.
The new management team, headed
by Tim Ryan, president, and Scott
Schwandt, vice-president, brings together
oilfield specialists with a wide range of
complementary skills. Mr Ryan commented,
“The new team in Houston is proud to be
the first representation of Barrett Steel in
North America. Our position here allows
us to serve the oil and gas equipment
manufacturing community with the backing
of an historically strong and proven company
in a strategically important location.”
Dave Godfrey, managing director of
Barrett Engineering Steels Division, is
enthusiastic about the prospects the new
Houston facility offers the group: “The
downturn in the UK construction market
demonstrated to us all too clearly that
we needed to refocus our strategy and
move into new markets. We had already
identified the oil and gas sectors as a
new international marketplace for us, and
this has been the impetus behind our
expansion into Houston. We are confident
that with our strong team of people, along
with our new facility, this initiative will be a
great success.”
Barrett Steel
– UK
Email:
info@barrettsteelep.comWebsite:
www.barrettsteelep.comMARMON/KEYSTONE’s
Cleveland
warehouse is the first location to switch over
to a new automated, paperless warehouse
processing system. The transition will reduce
order processing cycle time, resulting in more
timely service for customers.
A wholesale distributor of tubular
products for over 100 years, Marmon/
Keystone inventories more than 15,000
sizes and grades of carbon, alloy,
stainless and aluminium tubular and bar
products. Service centres and sales offices
are located throughout North America,
with corporate headquarters in Butler,
Pennsylvania.
According to Jay Powell, director
of e-commerce, “The automation will
increase both our quality and level of
output, enabling us to go one step further
in meeting our customers’ needs.”
Marmon/Keystone LLC
– USA
Email:
sales@marmonkeystone.comWebsite:
www.marmonkeystone.comWarehouse system for tubes