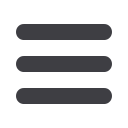

58
S
eptember
2011
www.read-tpt.com›
T
echnology
U
pdate
THERE is a strong trend for production
of seam-welded titanium tubes in the
tube market. Titanium tubes are used in
airline engines or frames and chemical and
nuclear power plants as they are very high
in corrosion resistance, light in weight and
high in strength. For each nuclear power
plant a volume of 300 tons of titanium tube
is required. So there is a lack of titanium
tube production capacity globally. The raw
material costs of titanium are 10 to 20 times
higher than comparable steels.
Even state-of-the-art stainless tube mills
are not able to combine highest tube quality
levels, production reliability and sufficient
production speeds at lowest scrap rates for
titanium tube manufacturing.
To follow this Rosendahl has developed
the new Titanium Tube Mill Series TH-G Ti.
These mills are designed for the production
of tubes for high security relevant issues
like heat exchanger products for power
generation. The main process steps
are fully re-engineered according to the
titanium alloy properties and end user
requirements: tube forming and calibration
to handle high spring back and secure a
smooth surface; welding and heat treating
processes that can avoid the restrictive
absorption of atmospheric gases, which
can lead to material embrittlement and
corrosion.
The dimension range for the TH-G Ti
Series goes up to 120mm in diameter and
can cover wall thickness values between
0.2 and 3mm.
The unique features of the TH-G Ti
Series are: Rosendahl hybrid-forming
for titanium tube production combines
the advantages of moveable and non-
moveable tooling; the introduction of a
high performance level to the titanium tube
manufacturing by use of high-end TIG-
plasma or laser welding technology; and
a fully integrated quality control system
including continuous thermographical
analysis of the welding seam.
Stop-and-go production for zero defect
welding for minimisation of scrap rates and
Rosendahl titanium tube mills are equipped
with in-line annealing systems, which can
also handle the speed range achievable with
laser welding systems.
Rosendahl Maschinen GmbH
– Austria
Email:
office@rosendahlaustria.comWebsite:
www.rosendahlaustria.comSeam-welded titanium tube mills
CARELL Corporation has introduced a
new HTH 20-150 four roll, double initial
pinch, plate bending machine designed
for manufacturing efficiency by using an
automated work cycle for the production of
cylindrical and radius segmental parts.
The Hi-Tech is designed to rapidly
produce radiused and cylindrical parts from
start to finish at the touch of a button.
Machines are engineered for high-speed
continuous production and easy set up
using durable mechanical and electric limit
devices. Add an auto loading and ejector
system and the Hi-Tech unit becomes a
powerful production tool for increasing
throughput while reducing handling time to
an absolute minimum.
The HTH Series boasts outstanding
standard features that include automated
bending cycles, top roll and pinch rolls driven,
hardened and polished rolls, rapid high speed
rolling velocity, automatic drop-end release at
end of cycle, compact space-saving design,
top support/deflector and sheet feed squaring
arm and back stop. Optional components
include: sheet-loading systems, cylinder
ejector systems, automated sheet alignment
systems, sheet pallet shuttle systems, and
special machine configurations for dedicated
production jobs.
Carell Corporation
– USA
Website:
www.carellcorp.comHigh-tech hydraulic rolling machine
Titanium tubes
from Rosendahl in
production (and right)
The Carell HTH 20-150