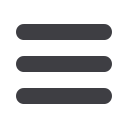

systems
Wire & Cable ASIA – May/June 2009
55
Drive nuts for
measuring machines
When developing its drive nut, Uhing conceived a non-positive linear feed
element that is successful as a drive element in measuring machines. “The secret
is its lack of play, a feature that is fundamentally inherent to the construction
of the drive nut,” explains Uhing’s head of marketing, Wolfgang Weber.
Drive nuts have three or four rolling rings being alternately pushed against
the surface of a plain shaft by spring force. These rings connect to the shaft
by friction.
Skewing the rolling rings results in their rolling off on the surface of the rotating
shaft at their pitch angle, thus generating a linear movement. This results in drive
nut and shaft acting like a nut and threaded spindle, but without threads.
The spring force required to produce the frictional connection automatically
reduces the theoretically existing play to zero, so there is no detrimental effect.
The drive nut instantly translates the smallest back and forth rotation of the shaft
into a movement to the left or right because there is no system-inherent play to
overcome.
The pitch of the drive nut varies in relation to the actual shaft diameter, which
is never constant over the entire stroke because the feed distance per shaft
revolution depends on the shaft diameter and the pitch angle of the rolling rings.
This is why there is no innate accuracy. For this reason, the actual position of the
drive nut must be monitored with a precise length scale in a measuring machine,
which is standard equipment in such machines.
“A release option, operated manually or pneumatically, is an additional advantage
for tool adjustment devices,” advises Wolfgang Weber. “Once the drive nut has
been uncoupled from the shaft, literally meaning the shaft has been released, the
tool or measuring instrument is quickly moved by hand. This prevents damage
to delicate components during test sample exchange, and measuring as such is
speeded up.”
The Uhing drive nut is quiet when running and requires little maintenance.
Joachim Uhing KG GmbH – Germany Fax
: +49 4347 90640
:
info@uhing.comWebsite
:
www.uhing.comTest system for
titanium rod
Magnetic Analysis Corporation,
a designer and manufacturer of
nondestructive test systems for
over 80 years, recently supplied a
multi-test eddy current/ultrasonic
system to inspect small diameter
titanium bars and rods (2.54mm to
31.75mm).
Testing criteria was AMS-2631B,
Class AA for the ultrasonic test
(aerospace specifications) and
typical eddy current inspection
standards for the eddy current test.
By combining eddy current
and ultrasonic technology in a
comprehensive inspection sys-
tem, superior test results can be
obtained as each technique is
used to detect the conditions that
it is best suited to find.
This particular system incorporates
Echomac
®
FD-4 ultrasonic instru-
mentation, an Echomac Rotary
which spins the transducers and
water couplant around the bar,
and a MultiMac eddy current
instrument and test coil.
The UT test uses one normal
incidence and two shear wave
transducers to inspect for surface
and near-surface defects such
as seams, spiral seams and light
cracks as well as inclusions and
deep voids.
The eddy current single channel
test complements the UT test by
detecting some very small surface
seams or pitting that are poor
reflectors of sound.
The test system also includes
air operated dual pinch stands
designed to drive and position the
test material accurately, a slide
and elevate platform to adjust the
UT Rotary, a water recirculation
system for the couplant, and
automatic markers.
The system is mounted on a welded
test bench and ‘learn controls’
are included to automatically
adjust the timing based on the
initial test piece.
Magnetic Analysis Corp – USA
Fax
: +1 914 699 9837
:
contactus@mac-ndt.comWebsite
:
www.mac-ndt.comUhing drive nuts for measuring machines
❍
❍