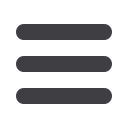

PRODUCT News
November 2016
MODERN MINING
45
SEW-EURODRIVE has supplied its X-Series
of versatile and powerful industrial gear
(IG) units to an ongoing coal terminal
expansion project in South Africa.
A long-standing relationship with the
coal terminal has seen the OEM’s scope of
supply to the upgrade project evolve from
supplying its traditional geared motors
to the latest X-Series IG units. “The intro-
duction of the X-Series IG units has seen
our relationship reach new heights over
the past five years, from the initial supply
of a few smaller geared units,” says SEW-
EURODRIVE’s Durban Branch Manager,
Casparus de Jager.
For this particular project, SEW-EURO
DRIVE supplied its X-170, X-180 and X-210
IG units. “We managed to receive an order
for a number of X-210 industrial gearboxes
ahead of some tough competitors,” notes
de Jager. “The scope of work included load
testing at our Durban branch.”
The reliability and availability of the
drive unit is critical in conveyor belt appli-
cations, as some conveyor belts only run
occasionally, while others operate 24/7.
“The X-Series provides robust, high-torque
drive solutions to meet the challenging
requirements of such systems,” comments
SEW-EURODRIVE’s Head of Engineering,
Andreas Meid.
“Our modular concept focuses on pro-
viding the correct IG units for conveyor
belt systems, even in tough operating con-
ditions and high ambient temperatures.
This means a reduction in total operating
costs for our customers, as well as reduced
maintenance costs,” he adds.
The X-Series has a torque range from
6,8 kNm to 475 kNm. It also features a
large number of accessories to allow for
maximum flexibility in meeting the diverse
requirements of a range of industries, and
a wide range of gear ratios for helical and
bevel-helical gear units.
Nearly any mounting position or shaft
arrangement on a driven machine can be
implemented. A reversible gear unit hous-
ing also facilitates variable installation.
Operational safety and ease of mainte-
nance have been taken into account in
terms of the robust housing, low-noise
gearing and cooling system in particular.
“Efficient project planning tools, includ-
ing the generation of 2D and 3D drawings,
as well as predefined drive packages
for conveyor drives and bucket elevator
drives, are also available,” says Meid.
The X-Series for belt conveyors com-
prises three-stage helical-bevel gear
units with special, horizontal housing for
improved heat dissipation and increased
SEW supplies gear units for coal terminal expansion
SEW-EURODRIVE has supplied its X-Series industrial gear
(IG) units to the coal terminal expansion project.
cooling capacity, thanks to an efficient
fan concept. This means that external
cooling units and a larger gear unit are
no longer necessary in most applications.
Applications include the cement and con-
struction materials industries, and surface
and underground mining.
SEW EURODRIVE, tel (+27 11) 248-7000
Bypass filters trialled at chrome mine
Condition monitoring specialist WearCheck
has now extended its fuels, lubricants, air
and coolants (FLAC) maintenance pro-
gramme to include unique bypass filters,
which minimise contaminants, thereby
extending the life of the oil and fuel.
The filters were initially trialled at a
chrome mine on three GHH machines
running air-cooled motors. Once proven
effective, the filters were then fitted to a
further 27 machines in the same mine. The
mine has already recorded savings of R1,7
million after paying for the implementation
of the WearCheck programme.
Also known as depth filters, the bypass
filters are bolted externally on each compo-
nent, and the oil or fuel of that component
passes through the filtration system, similar
– says WearCheck – to how an individual
dialysis machine would assist a patient to
filter his own blood.
The filters function best as part of a
comprehensive condition monitoring pro-
gramme, and, following the successful trials,
they are being widely installed on different
machines.
Fuel typically passes through three filters
– first the OEM water separator, next the
OEM diesel filter, and finally WearCheck’s
depth filter, which is last in line, and
which provides extremely fine microfiltra-
tion, screening particles between 0,5 and
1 micron in diameter.
WearCheck, tel (+27 31) 700-5460