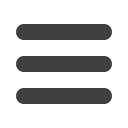

EuroWire – March 2012
56
News
Technology
Online recording of production data has
always played an important role in cable
production. In the past data was collected
separately at every single production line.
Therefore, simple plant computers were
used in combination with a printer for
extensively printing out the data at the end
of the production process. In particular, data
archiving was a major problem.
Nowadays, the measuring values are
recorded and stored digitally in real time.
This is especially important with regard
to the high capacity of the lines and
the related data volume. There are two
possibilities of data processing. On the
one hand, production data is measured
online and directly transferred to a central
quality assurance system. As there is often
measuring data of several production lines
available to the operator, a line computer is
quickly at its capacity limit.
That is why measuring data is first
collected and processed in processor
systems such as the Sikora Ecocontrol
before being transferred to a line
computer. Data can be stored daily,
batchwise but also reelwise. The processor
systems determine trends and statistics
over the entire production process and
document quality characteristics of the
product for defining Cp or Cpk values.
In addition, they provide information on
possible surface faults on the cable such as
lumps and neckdowns.
The online processing and recording
of quality characteristics is a significant
progress for cable production compared
to the past. Five years ago, a cable
manufacturer could make a statement
about statistical data. However, he had
not received details on the single values as
they were averaged.
Therefore, a cable could be shown
concentric in the average value, although
it was punctual eccentric. Only by means
of a cut cable sample could the operator
recognise that the core was eccentric in
the insulation and the cable did not fulfil
quality requirements.
Nowadays there are solutions such as the
so called cloud diagram, which graphically
present the distribution of short-term
variations of the eccentricity. The
information is stored and transferred to a
line control via serial interfaces or simply
by a USB stick. As a result, the operator
and the quality management continuously
have production data available for
monitoring processes and improving them
with the help of QS quality documentation.
Sikora AG – Germany
Fax
: +49 421 489 0090
:
sales@sikora.netWebsite
:
www.sikora.netData processing and
recording in extrusion lines
▲
▲
The cloud diagram is an alternative style visual view of the measurements being made at the processor system
Ecocontrol. With the help of the cloud diagram the distribution of the short-term variations of the eccentricity are
shown. The cloud consists of 5,000 dots, whereby each dot represents an actual single value of the eccentricity (value
anddirection).Theoveralldistributionoftheclouddiagrameasilyhighlightsthestandarddeviationoftheeccentricity