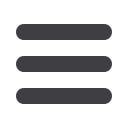

CAPITAL EQUIPMENT NEWS
JUNE 2017
8
improved and customers want to stick to
what they know in terms of maintenance.
Current BELAZ shipments of large trucks
with DC or AC depends on the size class,
with some long established 130 t and 220 t
models still seeing a lot of DC drive orders.
Why mechanical?
In terms of payload, Ingle argues that
mechanically driven trucks in the 182 t to
220 t size class have a 10-20 t empty weight
advantage over their electrically-driven
counterparts. “The lower mechanical empty
weight translates into more payload and
higher efficiencies,” says Ingle. Lavrenov
agrees, saying that less weight of the
components in a mechanical drive system
when compared with AC/DC drive systems,
translates into less truck weight.
When it comes to drivetrain efficiency,
Ingle also argues that for haulage trucks,
mechanical is the most efficient drive for
getting themost power from the engine to the
ground. “Electric drive truck manufacturers
talk about improved powertrain efficiency
of AC over DC but the fact is mechanical
drive is still more efficient than AC electric
drive. This has been proven in field studies,
and validated in the lab. The result is
mechanical drive can do more with equal
power or deliver the same performance with
less power. This translates into better fuel
savings,” says Ingle.
Meanwhile, mechanical drive trucks
do not burn fuel when retarding downhill.
Retarding forces drive need systems so fuel
to the engine can be turned off. Ingle also
says mechanical drive offers superior braking,
retarding and traction control. “Mechanical
drive trucks are recognised the world over
by miners and operators as better to operate
in poor underfoot conditions. Also, AC drive
has a dynamic retarding capability limit that
once exceeded, the truck starts to speed
up. Mechanical drive brakes / retarding can
bring a truck back into the desired operating
envelope,” says Ingle.
Ingle also argues that mechanical drive
trucks can generate and hold a higher peak
rimpull (torque) than electric trucks. “This
can be a bit confusing because electric trucks
offer optional final drive reductions that
improve peak rimpull at the cost of top end
speed. In addition, electric drive systems can
have a maximum electric current time limit
for how long they can pull peak torque.”
In a nutshell, Ingle believes that mechanical
drive offers lowest cost per ton. “Mechanical
drive delivers the best balance of production
and operating costs,” argues Ingle.
Why electric?
According to Egorov, application of electric
transmission results in much smaller number
of friction units (alternator, electric motors,
reduction gear units and control cabinets),
which saves up to 50% of oil compared
with a conventional mechanically-driven
RDT. “That simultaneously drives down
operational costs by up to 38% during
maintenance,” he says.
This view is shared by Lavrenov, who
argues that mechanical drive requires more
maintenance through oil changes, adding
that service life of major components is
shorter compared with electric drive.
Ingle says both drive options have engine
oil, final drive oil, steering and hydraulic
systems, but mechanical drive has a bit
more fluids for the transmission and oil-
cooled brakes. “But, an objective look at the
actual impact on operating costs shows this
only adds a very small amount of operating
cost to mechanical drive trucks and is
greatly offset by other mechanical drive
operating cost advantages,” argues Ingle.
Lavrenov adds that electric drive
has fewer major components than the
mechanical drive option, and this translates
into less potential failures. He also
argues that fewer components mean less
maintenance, which in turn translates into
higher availability and ultimately higher
productivity.
The trolley option is another key benefit
of the electric drive system, and Ingle
agrees to that fact. This is a major feature
of Hitachi’s AC-3 drive system technology
HAULING – RIGID DUMP TRUCKS
Hitachi pioneered the AC-3 technology to its RDT range in 2012. The AC-3 technology was
developed using advanced propulsion technology that also powers the OEM’s bullet trains in
Japan.
BELAZ is one of the OEMs which
maintains that trucks from 130
tonnes payload class and above
should be electrically-driven.