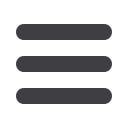

CAPITAL EQUIPMENT NEWS
JUNE 2017
7
manufacturers to develop DC electric drive
trucks with the launch of its 75 t 779 model
in the late 1960’s.
“After operating trucks at mines, we
concluded, at the time, that a mechanical
drive offered our customers the best
haulage solution and Caterpillar has
since steadily advanced mechanical drive
technology,” comments John Ingle, Large
Mining Trucks Marketing and Performance
Manager at Caterpillar.
Today, Caterpillar is the only manufacturer
that offers large (182 t) mechanical
drives. “Over the years, mechanical drive
has continued to move up in size as the
preferred drive solution over electric drive
as OEMs have been able to offer larger
capable mechanical drive systems.”
Cat’s viewpoint
According to Ingle, Cat mechanical drive
trucks have proven their value to miners
and are favoured in most applications. In
contrast to the notion that the electric drive
option is the better choice on the larger end
of the payload scale, Caterpillar offers the
widest range of mechanical drive trucks
from the 182 t payload and above class size.
The 136 t 785D starts what Caterpillar
terms its Large Mining Trucks and is a
mechanical drive truck. The 789D (186 t) and
the 793D/F (227 t) are also mechanical drive
trucks and are regarded the workhorses
of the industry, according to Ingle. Cat’s
mechanical drive goes as far as the 365 t
797F and Ingle argues that the mechanical
drive option remains the most productive
and lowest cost per ton drive system choice
for mining customers.
However Ingle notes that the OEM
also recognises that some customers
prefer electric drive in some size classes,
such as the 290 t and 330 t, which are
established around AC electric drive fleets.
Consequently, Caterpillar has invested into
the development of AC drive trucks since
the early 2000’s. “We have engaged key
customers with electric drive experience
throughout the development process to
gain their input on machine design and
performance,” says Ingle.
“Caterpillar is the only large mining truck
OEM that designs, produces and integrates
its own engines, powertrains, drive controls
and software. This is true for both Cat
mechanical and AC drive trucks and allows
us to optimise overall machine performance
and to provide product support for the entire
truck,” adds Ingle.
“While there are pros and cons to
either drive system, the bottom line is that
Caterpillar mining trucks, either mechanical
or electric drive, are designed to bring the
most value to our customers,” says Ingle,
adding that the choice depends on the size
of truck required and specific customer
preference.
BELAZ’s standpoint
According to Lavrenov, BELAZ is a true
proponent of the electric drive system for
the larger end of the payload scale. All its
models from 90 t and above are powered
by electric drivelines. “More specifically,
these are the trucks of 90, 110-130, 180,
200-220, 240, 360 and 450 t payload
capacity. The machines with 30, 45 and 55-
60 t are powered by mechanical drive,” says
Lavrenov.
“BELAZ believes that for 90 t and higher,
electric drive, and AC drive in particular,
provides better performance for customers
than mechanical drive,” says Alexander
Egorov, General Design Engineer at
BELAZ. Already the company has made
modifications to allow all its existing DC
drive models to use AC drive, while all its
new truck offerings have been designed
with AC drive.
However, the company says some of its
long-term customers have expressed their
desire to stick to DC drive. This is partly due
to the cost, and on the other hand, Egorov
says it’s because DC drive technology has
Caterpillar is the
only manufacturer
that offers large
(182 t and above)
mechanical drives.
Transmission and rear brake retardation systems come as standard on
Terex Trucks’ TR100 RDT to guarantee the optimum retardation for various
applications and conditions for safer control and shorter cycle times.