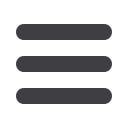

CAPITAL EQUIPMENT NEWS
JUNE 2017
2
EDITOR'S COMMENT
T
he plentiful list of choices for
each product on the market is
testament that original equipment
manufacturers (OEMs) strive to cater for
a diverse range of customer demands,
moving away from the conventional
one-size-fits-all approach. The manner in
which equipment is driven is no different,
with customers calling for various power
source configurations. So, which power
source should you opt for?
As you will see in the Hauling feature in
this edition of
Capital Equipment News
,
the mechanical versus electric drive debate
has always taken centre stage as far as
rigid haulers are concerned, especially
at the larger end of the payload scale.
But, this is surely a debate that goes well
beyond haulers and spreads across the
whole capital equipment spectrum.
For me, there are pros and cons for both
diesel/hydraulic and electric configurations.
The greatest benefit of the diesel/hydraulic
power-source is that it is a self-contained
with only fuel required. This allows the unit
to be located in remote locations where an
electric power source may not be available,
especially in Africa where remoteness of
sites is a common issue to contend with
for contractors. Another key benefit is that
there are no cumbrous electric cables to
deal with.
Plant equipped with diesel/hydraulic
power units obviously has added flexibility.
Operators can simply and quickly split
their system. If a particular plant is not
required, engines can be simply turned off.
An example of this would be if additional
further crushing or screening is not
required to produce a product, then units
not utilised in this process can be shut off,
reducing operator costs. This can also help
offset fuel and maintenance costs of the
operation.
Self-contained power units generally
are made up of a diesel engine, coupled
with hydraulic pumps, control valves to
operate the system and hydraulic motors.
This simple circuit eliminates the need for
expensive control panels, starters, wiring
cables and connectors. The circuit allows
for easier serviceability in that the diesel
mechanic that services your loader on site
may be able to service your track conveyor
or trommel. Electric systems generally are
much more complicated and may require a
trained service engineer.
On the other hand, the advantages of
electric-powered equipment over diesel
models extend well beyond the obvious
savings on diesel fuel. Electric-powered
equipment can significantly reduce
operating and maintenance costs, while
providing indomitable reliability and
uptime. There is general consensus that
electric systems are much more efficient
than their hydraulic equivalents and more
reliable regardless of the climate they are
operating in. Diesel/hydraulic power units
tend to be more temperamental in extreme
climates such as high altitudes.
Besides savings on diesel fuel,
electric-powered equipment eliminates
the costs and downtime associated with
maintaining a diesel engine and radiator.
Although an electric system may require
trained service engineers to carry out
maintenance, the regularity of service is
much less than that of a diesel engine and
will incur less downtime due to a blocked
filter, oil and coolant exchange, air filter
replacement, busted hose or a dusty
environment.
Meanwhile, current developments by
several OEMs are testimony that we are
further heading the electrical route, but I
believe the diesel/hydraulic options will
always have their place in the market.
DIESEL OR ELECTRIC?
THAT IS THE QUESTION
@CapEquipNews
Munesu Shoko – Editor
capnews@crown.co.za