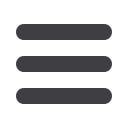

which it launched in 2014 in southern Africa. Hitachi pioneered the
AC-3 technology to its RDT range in 2012 with the launch of the
EH5000AC-3. The AC-3 technology was developed using advanced
propulsion technology that also powers the OEM’s bullet trains in
Japan. Hitachi Construction Machinery Southern Africa introduced the
new EH4000AC in the local market in 2014. Its trolley assist is a fuel-
saving method which is not available on mechanical drive trucks. It is
provided by an overhead catenary power supply supported by poles
mounted along main haul roads.
Another key benefit of Hitachi’s AC-3 drive system is that it comes
with a slip/slide control system. If the system senses slipping or locking
of rear wheels when travelling on slippery or frozen roads, it adjusts the
torques of the wheel motors accordingly, giving the truck better stable
travelling.
The AC-3 drive system also incorporates a pitch control system.
If this system senses pitching when travelling on bumpy surfaces or
an abrupt stop, it adjusts the torques of the wheel motors fittingly to
reduce pitching on the truck, ensuring better operating comfort and less
load spillage.
If the AC-3 Drive Control System’s side skid control function senses
oversteer or understeer from the newly equipped sensors on the unit,
it adjusts the torques of the wheel motors accordingly to stabilise the
side skidding. This gives the gigantic truck smoother movement and more
stable steering.
While dynamic retarding force is said to be another key benefit for
electric trucks, Ingle argues that this is only applied to the rear wheels.
“In many cases electric trucks can quote a high retarding power or fast
‘on paper’ retarding speed. In practical field applications, electric drive
retarding speeds are mostly reduced to provide protection from exceeding
the electric drive retarding capability envelope and because competitive
electric drive trucks do not have braking force on their front wheels like
Cat mechanical drive trucks (and the Cat 795F AC) which allows a more
effective braking force and good machine control – resulting in the ability
to better utilise potential retarding speeds,” he says.
Ideal conditions
According to Lavrenov, BELAZ’s argument that the larger end of the
payload scale, starting from around 130 t, needs AC/AC systems is based
on the fact that from this payload, trucks are involved in large-scale
mining where machines need to get over steep gradients, and electric
trucks are preferable.
He, however, notes that both drives need good haul roads with
gentle sloping, quality maintenance and service, responsible and skilled
operators and loading within the rated payload. “However, this is possible
in an ideal world only,” says Lavrenov.
“At BELAZ we are of the opinion that there are more variants and
configurations of operating conditions which suit electric trucks than
mechanical. For instance, electric drive is an obvious choice for deep pits
where trucks need to haul material from the bottom and get over steep
slopes,” says Lavrenov. He adds that from a production point of view,
mechanical trucks are notably slower on gradients when moving uphill
loaded.
Meanwhile, Ingle argues that historically DC drive trucks were used
in more flatter, moderate grade or easier applications, while mechanical
drive was used in poor underfoot and more severe hauls. “However, AC
drive has changed many of the past electric drive limitations. Today,
mechanical drive is still recognised as best for many applications, but
ultimately, it is more of a function from a mine’s point of view,” says Ingle.
Ingle, in conclusion, tells
Capital Equipment News
that when look-
ing to the future of drive technology for large mining trucks, the industry
tends to think of some sort of electric hybrid car approach. However,
Caterpillar continues to research energy recovery for both mechanical
and electric drive systems. Ingle notes that at this time energy recovery
for either of the drive solutions is not cost effective to implement.
b
CAPITAL EQUIPMENT NEWS
JUNE 2017
9