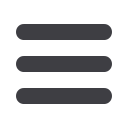

Technology News
www.read-tpt.com32
J
anuary
2015
Installation of brazing machine
THERMO King, a specialist in transport
temperature control systems for trucks
and trailers, has installed an automatic
brazing machine from EFD Induction.
The machine is employed to braze
vibration absorbers, components used
in the suction lines of air conditioning
and refrigeration systems.
Commenting on why EFD Induction
was chosen over alternative offerings,
Michael Corcoran, project manager
of Thermo King Ireland, said, “We
examined various proposals before
opting for the EFD Induction solution.
There were several reasons behind the
choice of supplier for this critical piece
of equipment. First, their solution made
technical and economic sense. Second,
the company has deep expertise in the
brazing field – especially in custom-
engineered solutions such as this
machine. And third, the fact that EFD
Induction is present throughout Europe
means we have considerable after-
sales support on our doorstep.”
The Thermo King machine features
a ‘separable’ coil design. “This use of
separable coils was decisive in winning
the Thermo King order,” said Bjørn
Røsvik of EFD Induction. “Indeed, it
was essential for the whole automation
process, making it possible to go from
manual brazing to a fully automated,
continuous production flow.”
The Thermo King brazing machine
is powered by an EFD Induction Sinac
18/25 generator. The Sinac model is
a ‘Twin’ version with two independent
power outputs, each with a split
transformer function, making it possible
to install separable coils. The full system
delivered to Thermo King includes an
automatic handling solution, a power
source and a chiller unit.
EFD Induction has manufacturing
plants, workshops and service centres
in the Americas, Europe and Asia, with
corporate headquarters in Norway.
EFD Induction AS
– Norway
Email:
sales@no.efdgroup.netWebsite:
www.efd-induction.comClamshell pipe cold cutter
DWT has enlarged the product range
of its pipe cold cutter up to 72". The
clamshell pipe cold cutter has been
developed for high metal removal rate,
a large adjustment range and an easy
setup in-situ. The portable clamshell
pipe cold cutter machine for pipe cutting
and bevelling avoids heat-affected zone
(HAZ) in the pipe cutting process.
Designed for heavy wall pipes in
heavy-duty applications, the high
working speed and quick set up
provide fast operation on-site. The
DLW-HD clamshell cutter is able to
operate safely and precisely in most
critical applications. A rigid frame
construction in combination with high
quality steel pinion gear and bearings
provide a rugged combination for
challenging work.
Features include cold cutters with
split-frame technology for endless
tubes; compact dimensions for use
in confined work spaces with limited
access; quick and safe clamping and
adjustment for pipeline welding; and
rigid pipe cold cutter for pipeline welding.
The application range of the DLW-HD is
for cold cutting of pipe from 48" to 72"
OD, and for wall thickness up to 100mm.
The split-frame cutters can be mounted
on assembled stretches of pipe. Special
applications such as remote control are
available for limited access in pipeline
welding.
DWT GmbH
– Germany
Email:
info@dwt-gmbh.deWebsite:
www.dwt-gmbh.deDetecting defects in copper tube
A FREQUENT problem for copper
tube producers is the presence of
foreign metallic inclusions, which
can lead to failures, particularly
in fluid transmission applications.
Magnetic Analysis Corp’s eddy
current Multimac
®
tester with an
additional magnetic inclusion detector
(MID) absolute channel provides a
convenient, reliable solution that can
detect inclusions as small as 3mg.
In many cases, the inclusion can
come from the material itself, which
may contain residual impurities from
continuous casting. In other cases,
such as finned tube, the inclusions
develop during the manufacturing
process, where small particles of metal
such as tungsten can break off from
fabricating tools and become imbedded
in the OD or even through the wall.
The MID option uses principles of flux
leakage technology. A magnetic dual-
coil test sensor consisting of one primary
winding, associated with a secondary
arranged in differential mode, and one
single absolute winding for detecting
metallic inclusions, is used.
A stable DC magnetic field is created
and, in its presence, a magnetic
particle on or within the non-ferrous
product passing through the test coil
will have the effect of distorting this
magnetic field. The distortion induces a
signal that is detected by the Multimac
electronics, analysed and displayed on
the monitor.
Magnetic Analysis Corp
– USA
Fax: +1 914 703 3790
Email:
info@mac-ndt.comWebsite:
www.mac-ndt.comCustomised brazing solutions