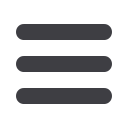

Technology News
www.read-tpt.com52
J
anuary
2015
Plasma annealing for automotive
and heat exchanger tubing
TUBES for the automotive industry
and heat exchanger tubing are made
of various materials and sizes. Copper,
galvanised steel, stainless steel, nickel
alloys, aluminium, or composite material
are all used in automotive and heat
exchanger applications. The sizes also
vary with ODs over 1" and over. For
such a varied product range one has
to adopt a variety of different annealing
and surface cleaning techniques.
Most of the above product range can
be heat treated and degreased also with
plasma. Plasma annealing has been
gaining increasing interest among tube
manufacturers in the automotive and heat
exchanger sector. Plasma annealing can
be used for production of tubes made
from the mentioned materials and sizes.
The advantage of using plasma as
opposed to a conventional furnace is high
rate of power input, which translates to
high process speeds. Plasma annealing
can be performed in-line with tube
welding or drawing substituting multiple
lines of a traditional tube furnace. It can
also be used for a brazing step in double-
wall tube production. Braking system and
fuel delivery tubing in a car are typical
applications where plasma can be used
effectively.
Plasma annealing or surface treatment
is conducted in a protective atmosphere,
which results in superior surface quality
of the finished tubes. Ion sputtering on
the material surface results in fine dry
surface cleaning and surface oxide
removal, which have proved beneficial
to applications with demanding surface
requirements. A range of inert gases or
their mixtures can be used for purging
of plasma machine. Hydrogen, nitrogen
and forming gas are the most commonly
used gases while helium and argon are
used in specific applications. The choice
of gas is important as it impacts the
surface finish of the processed material.
Many applications with demanding
surface quality can be found in heat
exchanger, aviation, automotive and
medical sectors.
Plasma treatment can be used
also for surface activation. Plasma
annealed tube surface remains active
and susceptible to coating, whilst still
in protective atmosphere. Plasma
annealer or plasma cleaner can
therefore run immediately in-front of
a coating or plating line in order to
avoid the use of chemicals for surface
preparation. Plasma annealer features
compact design, high energy conversion
efficiency and low gas consumption,
and gives the operator the ability to
target mechanical properties with a
great degree of accuracy. Rapid heating
and reduced time of recrystallisation
results in fine grain size with uniform
crystal structure. This in turn improves
material formability, and its susceptibility
to bending and further drawing.
Plasma annealer can cold start
production in few minutes and can be
stopped immediately. This avoids the
lengthy heating-up and cooling-down
times and associated energy costs
that are symptomatic of a conventional
furnace.
Plasmait GmbH
– Austria
Email:
info@plasmait.comWebsite:
www.plasmait.comPlasma annealing is gaining increasing
interest among tube manufacturers in
the automotive industry