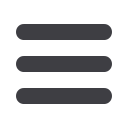

Technology News
www.read-tpt.comJ
anuary
2015
53
SMF enjoys faster throughput with
TruLaser Tube 7000
WHEN Leicester-based sheet metal
fabrication shop SMF UK had the
opportunity to replace its existing
Tubematic tube laser cutting and
profiling machine, the company had
no hesitation in returning to Trumpf.
Reliability, capability and support
steered the company towards a new
TruLaser Tube 7000, one of the first in
the UK. According to SMF, the upgrade
has brought many benefits, including
three to four times faster loading and
set-up.
SMF is a ten man subcontract
fabrication shop with a good spread
of work that includes everything from
electrical control cabinets and machine
guards, through to architectural
metalwork and parts for spacecraft.
Formed in 1990 by current managing
director Steve Morrison and his brother,
the company had been running a Trumpf
Tubematic successfully for many years.
“The machine was still very capable,
however, the advent of the RGF
(Regional Growth Fund) and 100 per
cent capital expenditure allowances
made the jump to the latest technology
more achievable,” explains Mr Morrison.
“And we’re very glad we did, it is a
wonderful machine.”
Whereas
operators
previously
struggled loading 7.5m lengths of tube
using the Tubematic, the TruLaser Tube
7000 can accommodate 9m lengths
with ease. Add the machine’s five-axis
head and its ability to accommodate
tube up to 250mm diameter rather
than 150mm previously, and it is easy
to see the positive impact made by
the TruLaser Tube at this progressive
manufacturing business.
Mr Morrison said: “We’re mainly using
the machine to produce point-of-sale
products for the retail sector, from both
round and square tube, largely from mild
steel with 1.2 to 3mm wall thickness.
However, we also process a reasonable
amount of 6mm stainless steel for the
architecture market. The machine cuts
all of our work superbly, and gives very
good yield.”
Installed in January 2014, the
machine – which is able to cut tube
with wall thickness up to 8mm – was
selected after SMF carried out a
benchmarking exercise involving a
number of potential suppliers.
“We looked at all of the alternatives, but
concluded that there wasn’t a machine
on the market that came anywhere near
the Trumpf tube machine for capability,”
said Mr Morrison. “The machine is
much quicker for programming and
loading than anything else we saw.
Furthermore, we can have three or four
jobs done on the TruLaser Tube 7000 in
the time it took to load one job on our old
Tubemaster. Also, whereas adjustments
to the rollers and bridge supports were
done manually on the Tubemaster, they
are all now completed automatically.”
Stepped rollers on the TruLaser
Tube 7000 that provide both support
and lateral guidance for the tubes
adjust automatically to the diameter of
the workpiece, while the self-centring
clamping jaws also adapt automatically
to the tube’s geometry. Furthermore, the
FocusLine regulation mechanism keeps
the laser’s focal position constant,
adjusting it automatically to suit the
type of material being processed and
its thickness. The machine’s software
activates the laser parameters as
necessary, depending on which tube is
being processed.
Three people at SMF are trained to
use the TruLaser Tube 7000, which
according to Mr Morrison has been
extremely reliable since it was installed.
“When SMF started in 1990, the
company had only a circular saw, a
radial drill and a welding machine. Now,
aside from its TruLaser Tube 7000, the
company has a Trumpf TruLaser 5030
fibre laser profiling centre, a Trumpf TCL
3050 laser cutter with 6kW resonator,
and a Trumpf TruMatic TC200R
punching machine. Also offered are
waterjet cutting, forming, welding and
powder coating.
Trumpf
– UK
Email:
sales@uk.trumpf.comWebsite:
www.uk.trumpf.comTruLaser Tube 7000