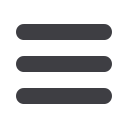

38
CONSTRUCTION WORLD
JUNE
2015
PROJECT PROFILE
high quality product is not only a significant
contributor to lower temperatures but the
peak temperatures also occur at a later age.
In addition to controlling heat of hydra-
tion, incorporating DuraPozz
®
produces
highly effective mix designs that enhance the
ultimate strength and durability properties
of concrete, while also aiding construction
with the improved workability and ‘flowa-
bility’ of the mixes.
Delivery capability
Lafarge South Africa’s extensive production
facility footprint (five fly ash plants and three
cement plants), means that it is in the unique
position of being able to guarantee supply
of large quantities of consistent high quality
cement and fly ash for major projects.
In addition, the company’s logistics
teams have a proud track record for ensuring
product is always available on a customer’s
project site no matter what delivery chal-
lenges may be encountered.
In complying with the contractor’s
requirement of an eight day estimated
usage stock on site, the project has not once
run short of cement or fly ash. The excel-
lent performance of the Lafarge produc-
tion plants has meant that it has not been
necessary to make use of any backup produc-
tion facilities.
The abnormal rainy season in early 2014
had a significant impact on the Metolong
Dam construction programme, which has
contributed to pushing back the anticipated
completion time from the second quarter to
the last quarter of 2014 (the contract time
was also extended by the total amount of
concrete needing to be placed increasing
from the estimates at the start of the
contract). Delivering to the Metolong project
site had its own challenges: in addition to
coping with border crossing delays, the final
18 km section of dirt road was frequently
flooded and damaged by the rains.
Apart from this, the nature of dam
construction leads to considerable vari-
ance in building material usage – when the
conditions were right, the contractor did
major non-stop pours and the consump-
tion of cementitious materials increased
dramatically. The contractor is extremely
complimentary about the success of
Lafarge South Africa in overcoming these
delivery challenges.
Environment impact
Ash Resources’ environmentally-friendly fly
ash plays two important ‘green engineering’
roles. It is a key ingredient in Lafarge South
Africa’s range of lower carbon footprint
cement products, and it has a direct role on
site for further extension of the Powercrete
Plus cement:
• Recycling a material that was originally
considered a waste product of the
Eskom coal-fired power stations, as
a value-added cementitious building
material.
• Reducing process and energy input
carbon dioxide (CO
2
) emissions. Each
ton of fly ash used in cement and
concrete saves approximately 1 ton of
CO
2
emissions and reduces dependence
on non-renewable raw materials.
(During the last 12 years, the use of Ash
Project highlights
In its building material supply performance for the
construction of Metolong Dam, Lafarge South Africa has
clearly demonstrated the meaning of the Lafarge Group’s
brand signature
Building better cities
. The company’s
‘One Lafarge’ true partnership approach with the main
contractor has technically, commercially and logistically
contributed innovative solutions to help the construction
of a project rather than merely being a commodity building
material supplier. The project will uplift a key economic
area around the capital city of Lesotho.
The longer term impact is that Lafarge has achieved a
significant technical breakthrough in the choice of cement
for RCC dam construction in Southern Africa. Its innovative
CEM II Powercrete Plus cement offers:
• Strength performance on a par with traditional CEM I
products.
• Reduced heat of hydration.
• Better workability.
• Versatility on site through being able to be blended
further with fly ash to meet project requirements for a
cost-effective variety of mixes.
• Better flowability of CVC mixes over long distances
from a fixed on site batch plant.
• Creates concrete with essentially the same matrix as
with a CEM I cement but is denser, more durable and
impermeable.
Resources’ fly ash by the local cement,
readymix and construction industries,
has saved South Africa in excess of
17,5 million tons of greenhouse
gas emissions).
• Reducing the consumption of non-
renewable natural resources.
• Reducing the size of power station
landfill sites.
• Improving concrete durability, prolonging
the life cycle of concrete structures.
Health and safety
Safety is a non-negotiable number one
priority at Lafarge South Africa and includes
contractors working on the company’s sites
as well as transport contractors. Contractor
drivers have embraced the Lafarge safety
training, as well as the rigorous procedures
for checking the road worthiness of road
tankers before they are allowed to be filled at
the supplying plant.
Lafarge South Africa strives to create a
partnership with transporters in the drive for
excellence in safety performance. In this way,
the company is viewed as a trusted advisor
on safety procedures rather than being
viewed as merely a commodity supplier. The
drivers’ safe working behaviour also makes
them an ambassador for the Lafarge brand.
Ash Resources has supplied the Metolong
Dam project for the last two years without a
Lost-Time Injury at its Lethabo production
plant or to its transport contractors. Simi-
larly, Lafarge Lichtenburg Cement Works,
in the North West Province, has supplied
Powercrete Plus without a Lost Time Injury
on the plant or to its transport contractors.