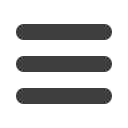

36
September 2012
www.read-eurowire.comS
UK
Focus on
July 2013
-eurowire.comThe new appointments come on the
back of a period of sustained growth
for
Meltech,
based
in
Blackburn,
UK. Founded more than 30 years
ago, it stands out as a North West
engineering company which weathered
the worst effects of the downturn in
UK manufacturing by developing a
determined approach to worldwide
exports, focusing on blue chip customers
and harnessing its considerable technical
strengths.
In recent years, Meltech has picked up
orders from multinational companies
such as Technip, Oceaneering and Parker
Scanrope, delivering projects in Russia,
USA, Europe and South America.
Meltech Group has now been organised
to emphasise its four operating divisions,
three of which – Heat Treatment, CRE,
(Continuous Rotary Extrusion) and Cable
Machinery – are product driven. The
fourth, TPS (Total Process Solutions),
offers feasibility and project planning,
project management, QHSE, reporting
and on-site contract management in
support of major contracts fulfilled by the
others.
Whilst Mr Drever and Ms Williams will
have MD responsibilities for individual
companies within the group, their
expertise will be harnessed as appropriate,
across all divisions within the group.
Meltech Engineering – UK
Website
:
www.meltech.co.ukOil resistance in cables
Cables demonstrating various degrees
of oil resistance are specified for use in a
number of applications such as railways,
shipbuilding, offshore platforms and wind
turbines.
Often the most difficult performance
parameter for the cable sheath is the
retention of mechanical properties after
immersion in IRM902 and IRM903 oils at
elevated temperatures. Standards for
offshore drilling rigs may also require
resistance to oil drilling muds, which
can be more demanding in this respect.
Cables used in these applications also
have the added difficulty of having to
be installed and to operate in very cold
climates.
Some typical standards are BS7655-1.4
2000 Insulation and sheathing for
cable
elastomeric
cables,
BS7655-1.5
2000,
Insulation
and
sheathing
for
cables - coil end leads, BS7655 2.0
2000
Sheathing compounds for ships
wiring and offshore applications, BS7655
2.6 1997 Ordinary duty oil resisting types,
EN50306-1 2002 Railway rolling stock cables
having special fire performance, EN50305
2002 Railway rolling stock cables - thin wall,
EN50264-1 Railway rolling stock cables -
standard wall, and IEC 60092-359 Sheathing
materials for shipboard power and telecom
cables.
These types of cable are usually made
using rubber as the sheathing and
insulation. However, there are a number
of companies who are keen to enter
this market who do not have the use of
the continuous vulcanisation (CV) line
necessary to cure the rubber. In addition,
even in those companies that have this
technology, there can be a shortage of
capacity and it is expensive to install
more.
SX-0620 is a new grade of crosslinkable
oil resistant sheathing compound, which
has exceptional resistance to IRM902 and
IRM903 and, at the same time, is flexible
even at cold temperatures. It employs
the Sioplas crosslinking technique, which
also means that it can be processed on
conventional cable extrusion equipment.
An added benefit is that because the
Sioplas process is a low pressure process,
it is not necessary to use hard rubber
insulated cores to avoid deformation
during the CV process. If the applicable
standard allows Sioplas crosslinked or
even thermoplastic insulated conductors,
these can be used instead, thus making
important savings on processing costs
and possibly CV capacity.
▲
▲
Chairman Marcus Moir, centre, with Peter Drever
and Helen Williams
Photo: bigstockphoto.com – ‘Ranoch Moor, Scotland, UK’ by Alexander Morrow