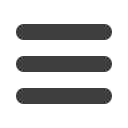

Technical article
July 2013
42
www.read-eurowire.comWire and cable and electrical equipment
standards were not implemented until
later in the century. Standards support the
minimum properties required for safety
and performance.
Every three years the NEC is significantly
revised to keep pace with technology
and further enhance protection against
electrical fire and shock hazards. The
absence of, or poorly written, standards
would significantly reduce the quality
of life on earth. Good standards serve
as a barrier to sub-standard products.
Standards should bring value, be effective
and not act as a barrier to free trade. You
can help this process.
2.1.2 Value of Standards
Development
:
Standards are developed by a consensus
reached based upon input from a variety
of interests. Producers, users, testing
companies and customers each bring their
perspective to the standards development
process. This process adds value because
it develops standards that are effective,
relevant, and credible based upon the
integrity of the developers
(5)
.
Advances
in
technology
influence
standards. They evolve as wire and cable
(W&C) technology changes. This makes all
of us, as producers and users, important,
with our input being vital for good
standards to bring value and benefits.
Wire and cable products meet demanding
electrical test, physical, mechanical and
chemical property performance criteria for
a variety of rated temperatures.
Standards development revolves around
generation of performance data and
information to permit safe practices
during installation, testing and usage of
wire and cable products. We expect these
products to last for 30 or more years.
ASTM was cited by The 1947 President’s
Conference on Fire Prevention
(6)
for its
recognition that performance rather than
specific materials should decide the future
course of fire safety. Performance allows
for new materials developments to raise
safety standards to the next level.
2.1.3 Benefits of Standards
Development
:
a
Safety
– The NEC and ASTM, among
others, provide practical guidance
to help safeguard employees and
the public from hazards during
the
installation,
operation,
and
maintenance of electric supply and
communication lines and associated
equipment.
The
NEC
covers
a
broad
range
of
electrotechnical
areas, including storage batteries,
transformers, conductors, switchgear,
circuit breakers, physical clearances,
cable terminations, safety warning
signs,
and
protective
clothing
for
workers
installing
electrical
equipment.
To provide for electrical safety,
methods that determine the level of
insulation resistance to transmission of
electricity through various substrates
have been developed
(7)
. One measure
is volts per mil determined by ASTM
D149
(8)
. This method is a measure of
the dielectric breakdown voltage and
dielectric strength of the insulation.
The value is high for a good insulation
material.
Another measure is dielectric constant
(DC) or dissipation factor (DF)
measured by fluid displacement using
ASTM D1531
(9)
. Electrical resistance to
breakdown by treeing in insulation is
measured by ASTM D3756
(10)
. The value
is low for a good insulation material.
ASTM D4872
(11)
is a test method for
dielectric testing of wire and cable
filling compounds. The inclined plane
tracking and erosion test, ASTM
D2303
(12)
, or the dust and fog tracking
and erosion resistance test, ASTM
D2132
(13)
, evaluate tracking resistance
on the contaminated surface of an
insulation material.
b
Physical Properties and Chemical
Resistance
–
Tensile
strength,
elongation low temperature and room
temperature impact, crush resistance,
and additionally, oil, gasoline, and
ozone resistance can be evaluated for
the operating environment. Examples
of performance standards that contain
these performance properties are
ASTM D470
(14)
, UL 44
(15)
and UL 83
(16)
.
c
Flame and Smoke performance
–
Various levels are attained depending
on the required level of safety. For
cable, UL 44 contains FT1 – dripping
particles, FT2 – horizontal and FT4
vertical tray fire tests for example.
Additional examples of W&C fire and
smoke performance tests are shown in
Table 1.
Electrical cable product fire safety
performance has been evolving. Fire
safety is partly based upon control of
ignition, the rate of heat released, and
flame spread or smoke released during
a fire. These are critical measures and
are evaluated by UL 1685
(25)
and ASTM
D5537
(23)
, for example. The amount
of heat released determines how
quickly a fire can spread. Greater and
more rapid heat release will overcome
some fire resistant additives. More
heat released creates a greater fire
fighting challenge for firefighters who
arrive on the scene. Controlling the
amount and intensity of the heat and
smoke released will allow trapped
people more time to escape safely
and property damage may be less
extensive.
The level of smoke can obscure vision
and inhibit or prevent people from
escaping from a fire scene. There are
standards designed to measure the
level of smoke through standards
such as UL1685
(25)
, ASTM E662
(24)
, or
smoke obscuration measured by ASTM
D5424
(21)
. ASTM Standard D5485
(22)
, first
issued in 1994, addresses the corrosion
of electronic systems as a result of fire
damage. Loss of electronic systems can
affect alarms and other critical systems
in buildings. These revised and newer
standards reflect the evolution toward
better fire safety.
d Temperature performance –
75
or 90ºC rating defines performance
of cable for overload capability, or
operating temperatures for example.
2.1.4 Electrical Fire Safety
(27)
Report
issued by the US Fire Safety
Administration
The Problem
: During a typical year,
home
electrical
problems
account
for
26,100
fires
and
more
than
$2 billion in property losses. About half
of all residential electrical fires involve
electrical wiring. Statistically, December
and January are the most dangerous
months for electrical fires. Fire deaths
are highest in winter months with
more indoor activities, and increases in
lighting, heating, and appliance use. The
bedroom is the leading area of fire origin
for residential building electrical fires.
However, electrical fires that begin in the
living room/family room/den areas result
in the most deaths.
The Causes of Electrical Fires
: Most
electrical distribution fires result from
problems with “fixed wiring” such as faulty
electrical outlets and old wiring. Problems
with cords (such as extension and
appliance cords), plugs, receptacles, and
switches also cause many home electrical
fires. Light fixtures and lamps/light bulbs
are also leading causes of electrical
fires. Many avoidable electrical fires can
be traced to misuse of electric cords.
These include overloaded circuits, poor
maintenance, and running the cords under
rugs or in high traffic areas for example.
2.1.5 Marketing Considerations
Standards are necessary for business
success. Having people who are standards
experts in your organisation is essential.