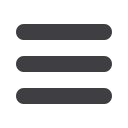

THE UK OFFSHORE OIL AND GAS FABRICATORS DIRECTORY
2016
page 44
Projects and Markets
Expertise
• Complete topsides delivered on EPC basis,
including process/utility/accommodation
modules. The existing facilities can cope with up
to 20,000 tonnes
• Jackets for oil, gas and offshore wind projects,
including piles
Mass Manufacturing
BiFab, in collaboration with universities and education
institutes, commissioned a detailed study, during
the construction of the two jacket substructures for
the Beatrice project, on the various manufacturing
processes involved. Its aim was to maximise the
total number of substructures that could be built
in a year. The study is now complete and we are
aware of the cost of the proposed new buildings at
our Methil, Fife facility. This proposal would take
BiFab’s current production capacity at Methil from
60 structures to between 100 and 150 structures per
year. The company intends to have this new facility in
operation by the end of 2016.
BiFab believes that Scotland’s proximity to the North
Sea and Baltic Sea, together with the experience
gained from the above projects, including expertise
available at the University of Strathclyde and other
educational institutions, places it in a unique position
to develop the world’s first mass manufacturing
facility to produce large offshore substructures cost
effectively. BiFab recognises that this is an expanding
market and is very keen to see this kind of technique
used more widely throughout the offshore
wind industry.
Innovation – New Jacket Design BiFab/Atkins
Based on experience gained from recently completed
offshore wind farm projects, BiFab and Atkins have
developed their own jacket substructure to support
offshore wind turbine generators. This design is jointly
(50:50) patented and capable of supporting a range
of turbines from three to eight megawatts in water
depths 15 metres down to 80 metres. It is a lightweight
structure, with potential savings in both weight and
manufacturing costs, along with the potential to load-
out more structures per barge due to the reduced
footprint at the base of the jacket.