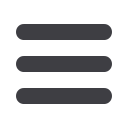

wire
2016
show
4
th
- 8
th
April
March 2016
125
www.read-eurowire.com➣➢➣
➣➢➣
HFSAB’s reputation is as a specialist in
lead extrusion equipment and know-how
for trouble-free lead sheathing of cables,
providing a perfect moisture barrier.
Lead extruders from HFSAB have all been
designed, manufactured and assembled in
Sweden over the last 50 years.
The lead extruder is horizontal, oor
standing, easy to install and maintain, fully
automatic and extremely reliable with its
state-of-the-art control system enabling
continuous operation for weeks with
little or no variation in temperatures, wall
thickness or concentricity. The lead wall
thickness can be kept to a minimum with
corresponding savings in lead.
A range of high quality and energy-
e cient melting pots are available for
10, 18, 35 and 60 tonne capacities. Also
available from HFSAB are cable-stripping
machines, the CRRS and model H. Both
are capable of removing individual
layers without causing any damage to
the subsequent layer below, enabling
the outer jacket, lead sheath or triple
layer XLPE to be reapplied and the cable
repaired.
The CRRS is used for the removal of outer
sheathing materials such as HDPE with or
without a bonded thin aluminium metallic
sheath, PE, PVC or lead. The CRRS has a
cable diameter range from 30 to 180mm
and is capable of removing 220kV XLPE
insulation up to a thickness of 25mm. The
model H has a smaller cable diameter
range of 10 to 125mm and can remove
XLPE thicknesses up to 15mm.
H Folke Sandelin AB – Sweden
Website
:
www.hfsab.comHolton Crest
Stand: 11H39
A European manufacturer has chosen
Holton Crest for the supply and
implementation
of
a
full
turnkey
production line. Equipment includes
the latest HC4000 dual axis 500kW
rotary extruder, full product condition
equipment, integrated power and control
systems, and two automatic changeover
double drum coilers for continuous
production
and
perfect
product
presentation.
Holton’s controlled expansion continues
with over €5 million of current orders for
the latest range-topping HC2200 and
HC4000 machines at various stages of
manufacture at the UK facilities.
With Holton’s ‘in production’ twin axis
vertical and horizontal tooling adjustment,
high
production
speeds
can
be
maintained across a range of products and
pro les, satisfying the immediate need but
also future demands.
High
service
factory
components
help with reliability, but underpinning
everything is the design.
Every detail has to be looked at on its
merits and nothing is o limits, from
operators to maintenance, speed to tool
life, and tool change times to warm-up
times.
“Current orders are fantastic, particularly
to be selected on technical merit,
but to meet the need for continuous
technical developments into the future
we identi ed the requirement and
started our new technical graduate
▲
The HC2200 from Holton Crest